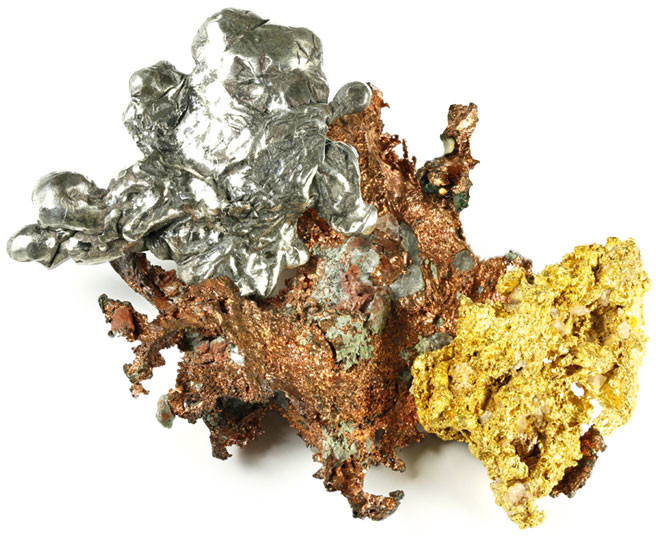
Rostschutz mit Röntgenstrahlung
Das EDX-7200 als Schweizer Taschenmesser in der Galvanik-Qualitätskontrolle
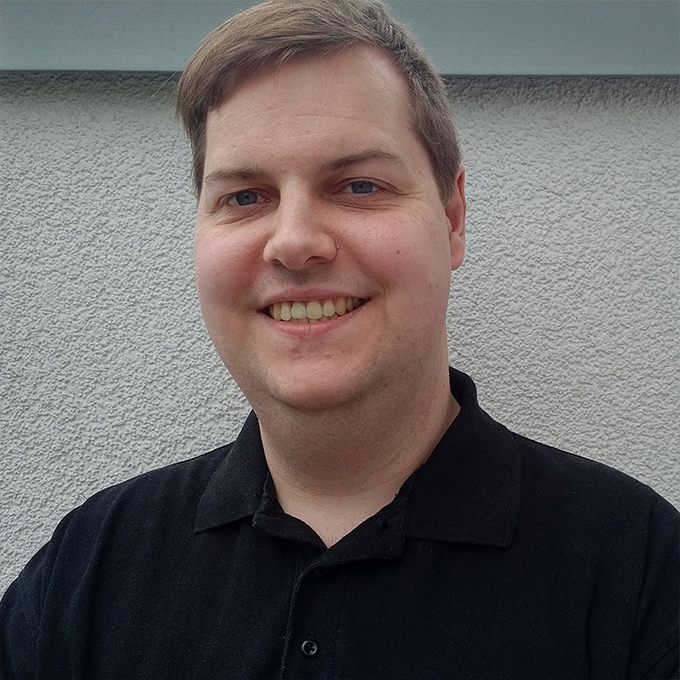
Dr. Benjamin Thomas, Shimadzu Europa GmbH
Galvanisch beschichtete Produkte sind aus unserem Alltag nicht mehr wegzudenken, vom rhodinierten Ehering bis zum verchromten Motorradauspuff. Viele analytische Fragestellungen rund um Galvanik – von der Zusammensetzung des Galvanikbades bis zur Dicke der aufgebrachten Beschichtung – lassen sich zerstörungsfrei mit energiedispersiver Röntgenfluoreszenz-spektroskopie beantworten. Somit vereint ein Gerät viele verschiedene Applikationen.
Die energiedispersive Röntgenfluoreszenz (ED-XRF für Englisch „energy-dispersive x–ray fluorescence“) ist ein zerstörungsfrei arbeitendes Analyseverfahren, mit dem die Elementzusammensetzung einer Probe analysiert werden kann. Dabei wird die Probe mit Röntgenstrahlung belichtet. Die Energieverteilung und Flussdichte dieser Röntgenphotonen kann durch Spannung und Stromstärke an der Röntgenröhre und das Zwischenschalten von Absorptionsfiltern für die jeweilige Analyse optimiert werden.
Das Prinzip lässt sich am besten anhand des Bohrschen Atommodells (Abbildung 1) beschreiben: Durch die Bestrahlung werden Elektronen aus den Atomorbitalen („Schalen“) der in der Probe enthaltenen Elemente herausgeschlagen (1). Es entsteht ein sogenanntes „Loch“ (2). Die für diese Anregung benötigte Energie hängt von der Ordnungszahl des jeweiligen Elements ab. Das angeregte Atom kehrt nun in den energetischen Grundzustand zurück, indem das entstandene „Loch“ durch ein Elektron aus einer höheren Schale gefüllt wird (3).
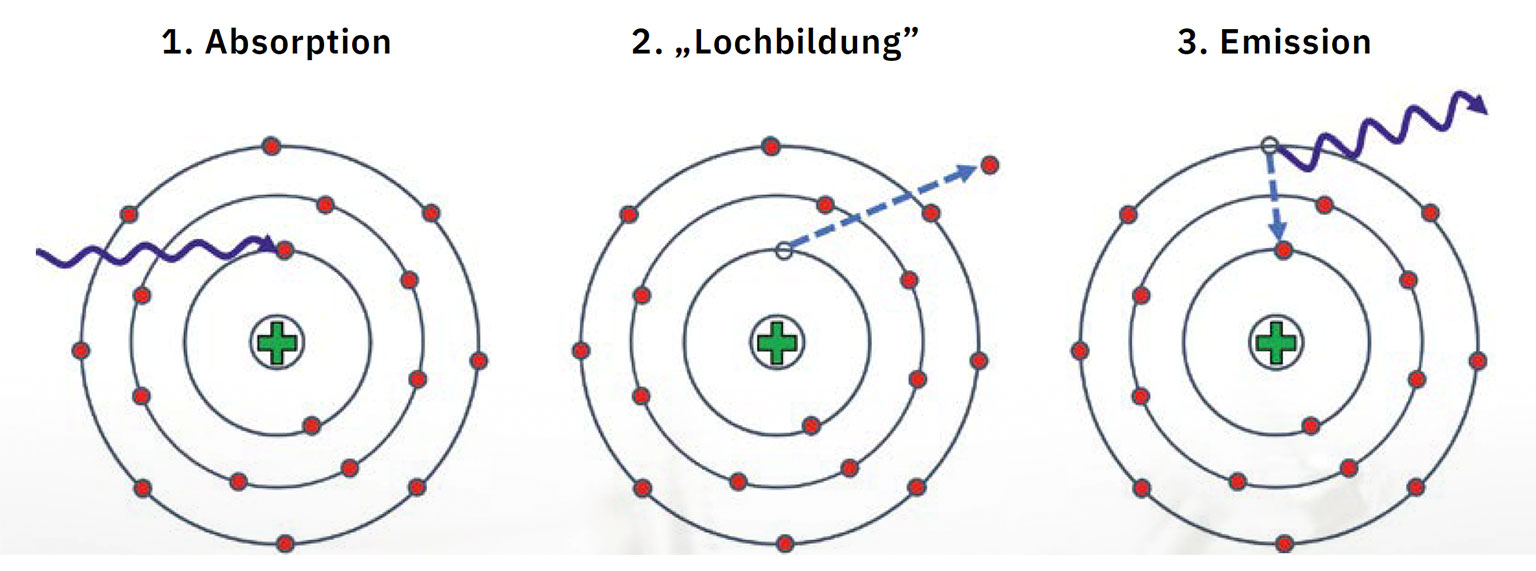
Abbildung 1: Röntgenfluoreszenz am Bohrschen Atommodell erklärt
Gemäß dem Energieerhaltungssatz muss dabei die überschüssige Energie in Form von Licht abgegeben werden. Die Energiedifferenz zwischen zwei Schalen – und somit die Energie des abgegebenen Photons in Kiloelektronenvolt (keV) – kann quantenmechanisch berechnet werden und ist charakteristisch für jedes Element. Aus dem Spektrum kann daher die Elementzusammensetzung der Probe berechnet werden, bei bekannter Zusammensetzung jeder Schicht aber auch die Schichtdicken. Die Röntgenstrahlung dringt dabei je nach Zusammensetzung und Dichte bis zu 100 µm in die Probe ein.
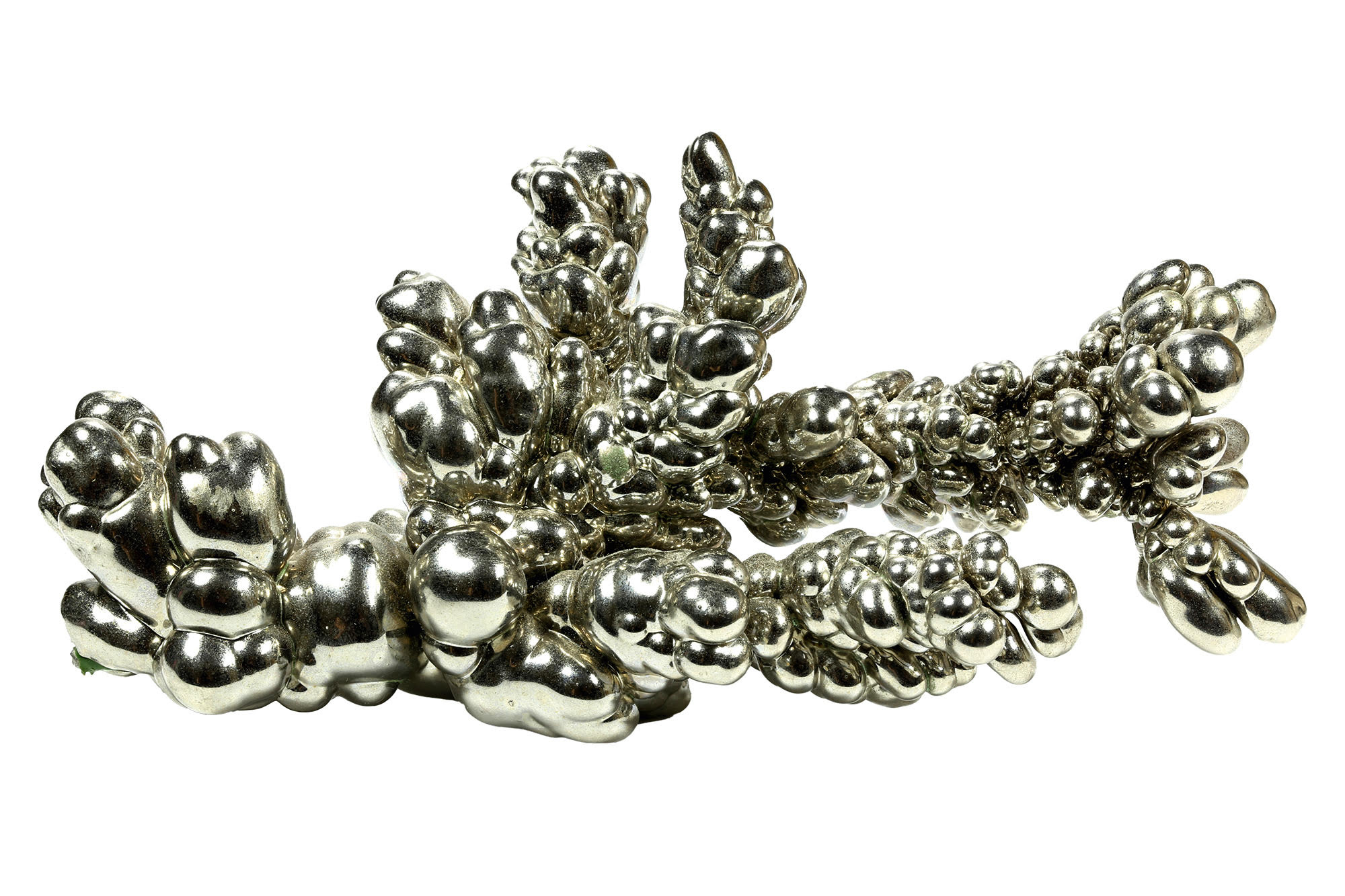
Korrosion
Viele Alltagsgegenstände und auch Baumaterialien werden aus metallischen Werkstoffen gefertigt. Die meisten Metalle liegen in der Natur in Form von Erzen vor, also in chemischer Verbindung mit Sauerstoff (Oxide) oder Sauerstoff und Kohlenstoff (Carbonate). Die daraus gewonnenen Metalle sind entsprechend anfällig für Reaktionen mit Sauerstoff oder Säuren und kehren bei ungeschütztem Kontakt mit Luft und Feuchtigkeit auf lange Sicht in ihren Ursprungszustand zurück – sie korrodieren.
Korrosion ist ein elektrochemischer Prozess, bei dem Wasser als Elektrolyt wirkt. Dabei gibt das Metall Elektronen an im Wasser gelösten Sauerstoff ab (Abbildung 2). Es bilden sich negativ geladene Hydroxidanionen und positiv geladene Metallkationen, die im Wassertropfen gelöst sind. Daraus wiederum entsteht unlösliches Metalloxid, das sich auf der Oberfläche des Metallkörpers abscheidet oder mit dem Wassertropfen abgewaschen wird.
Während einige Metalle, wie z. B. Aluminium, bei Luftkontakt eine durchgängige, stabile und so vor weiterer Korrosion schützende Oxidschicht ausbilden, lagern sich die Oxide anderer Metalle, wie etwa Eisen, locker und wasserdurchlässig ab. Somit „frisst“ sich die Korrosion regelrecht durch den Metallkörper, bis die Struktur des entsprechenden Bauteils nachgibt. Säuren sowie Kontakt mit anderen Metallen („Bimetallkorrosion“) begünstigen diesen Vorgang.
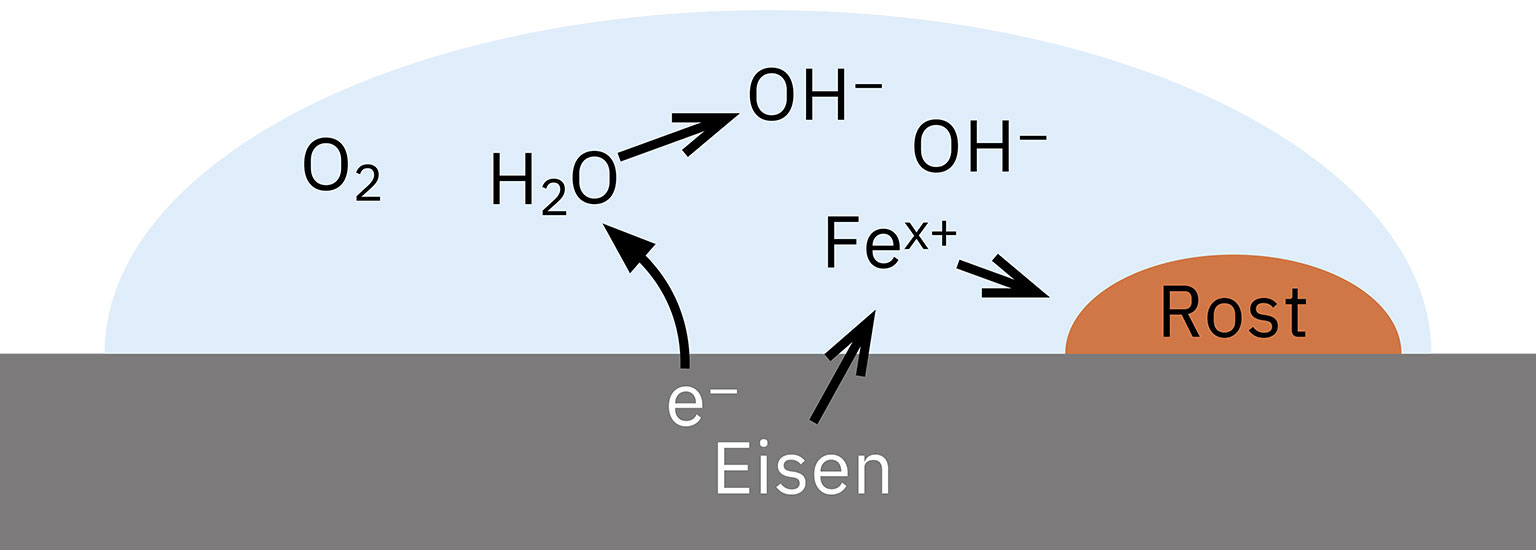
Korrosionsschutz
Beim Korrosionsschutz gibt es verschiedene Ansätze (Tabelle 1). In den meisten Fällen wird der Korrosionsschutz durch Beschichtung mit anderen Metallen, Harz oder einer Kombination aus beidem („Duplex-System“) erreicht. So begegnen uns im Baumarkt beispielsweise „feuerverzinkte“, also in einer Zinkschmelze beschichtete, Schrauben; in der Küche finden wir galvanisch vergoldetes Besteck und auch der Ehering aus Weißgold ist in der Regel galvanisch rhodiniert, d. h. durch eine dünne Rhodiumbeschichtung vor Korrosion geschützt.
Dabei hat jede Technik ihre eigenen Vor- und Nachteile: Der Schutz durch Beschichtung mit einem edlen Metall (z. B. Vergolden) ist in der Regel langlebig, da die Schutzschicht chemisch stabil ist. Bei Kratzern oder fehlerhafter Beschichtung ist die Korrosion allerdings im Vergleich zum ungeschützten Werkstück sogar beschleunigt. Eine Beschichtung mit unedlem Metall (z. B. Verzinken) schützt auch indirekt bei Kratzern, da die Beschichtung sich anstelle des Grundmaterials auflöst. Dafür ist sie aber weniger langlebig.
Prinzip |
Wirkweise |
Vorteil |
Nachteil |
Beispiel |
Beschichtung mit Edelmetall |
Schutzschicht nicht anfällig für Korrosion |
Langlebigkeit |
Beschleunigte Korrosion bei Beschädigung |
Vergoldung, Verchromung |
Beschichtung mit unedlem Metall |
Schutzschicht fungiert als Opferanode |
Schutz auch bei Beschädigung |
Schutzschicht löst sich langsam auf |
Verzinkung, Opferanoden am Schiffsrumpf |
Beschichtung mit Kunststoff |
Schutzschicht nicht anfällig für Korrosion |
Keine Bimetall-Korrosion |
Geringe mechanische Stabilität |
Teflon-Beschichtung, Schutzlack |
Anlegen von Fremdstrom |
Verlorene Elektronen kontinuierlich „nachliefern” |
Verschleißfrei |
Nur im Großmaßstab praktikabel |
Brücken, Pipelines, Schiffsaufbauten |
Galvanikverfahren
Bei galvanischen Verfahren wird ein elektrisch leitfähiges Werkstück durch elektrochemische Abscheidung von Metall aus einer Elektrolytlösung beschichtet. Dabei werden beide Metalle in ein leitfähiges Bad getaucht und ein Gleichstrom angelegt (Abbildung 3). Das zu beschichtende Werkstück dient hierbei als Kathode, das Ausgangsmaterial der Beschichtung als Anode. Durch den Stromfluss wird das Ausgangsmaterial nach und nach abgebaut und geht in Form von Ionen in Lösung. Alternativ wird in der Technik oft eine unlösliche Anode aus Edelstahl eingesetzt und das Beschichtungsmaterial in Form von löslichen Salzen zugeführt. Die im Galvanikbad gelösten Ionen werden in beiden Fällen durch den am Werkstück anliegenden Strom wieder zum Metall reduziert, das sich in Schichten auf dem Werkstück ablagert.
Die großtechnische Anwendung der Verfahren ist sehr komplex. Die chemische Zusammensetzung des Bades muss genau überwacht werden, ebenso die Stromstärke und Beschichtungszeit. In der Praxis sind oft mehrere verschiedene Schichten nötig, um einen mechanisch und chemisch stabilen und langlebigen Korrosionsschutz zu erreichen. Die folgenden drei Beispiele zeigen, wie die EDX-Spektroskopie zur Kontrolle der Ausgangsmaterialien, Zwischen- und Endprodukte eingesetzt werden kann.
Beispiel 1: Zusammensetzung der Grundlegierung
Die möglichen Beschichtungen, benötigten Parameter und Vorbehandlung hängen vom Material des zu beschichtenden Werkstücks ab. So kann Edelstahl zum Beispiel auf Hochglanz poliert und direkt verchromt werden, während andere Stahlsorten zunächst verkupfert und vernickelt werden müssen, um eine Grundlage für die finale Chromschicht zu schaffen.
Mittels EDX-Spektroskopie lässt sich die Zusammensetzung einer Legierung einfach bestimmen. Je nach Anzahl der erwarteten Elemente reicht eine Messzeit von 30 Sekunden oft aus. Ein qualitativ-quantitatives Ergebnis kann dabei auch ohne Kalibration ermittelt werden. Da die Position der elementspezifischen Linien bekannt ist, können alle gemessenen Linien automatisch zugeordnet werden. Anhand der Intensitätsverhältnisse wird dann eine Verteilung ausgegeben.
Da chemische Wechselwirkungen unter den Legierungselementen die Quantenausbeuten für jedes Element beeinflussen können, kann die Präzision des Ergebnisses durch Kalibration mit entsprechenden Standards verbessert werden. In der Regel ist die qualitativ-quantitative Messung ein erster Schritt. Auf Basis der gefundenen Elemente wird die Probe dann mit einer quantitativen Methode erneut gemessen, um die genaue Zusammensetzung zu ermitteln (Tabelle 2). Tabelle 2 zeigt die ohne Kalibration ermittelten Ergebnisse der Aluminium-Silizium-Legierung aus Abbildung 4 im Vergleich zu den zertifizierten Werten.
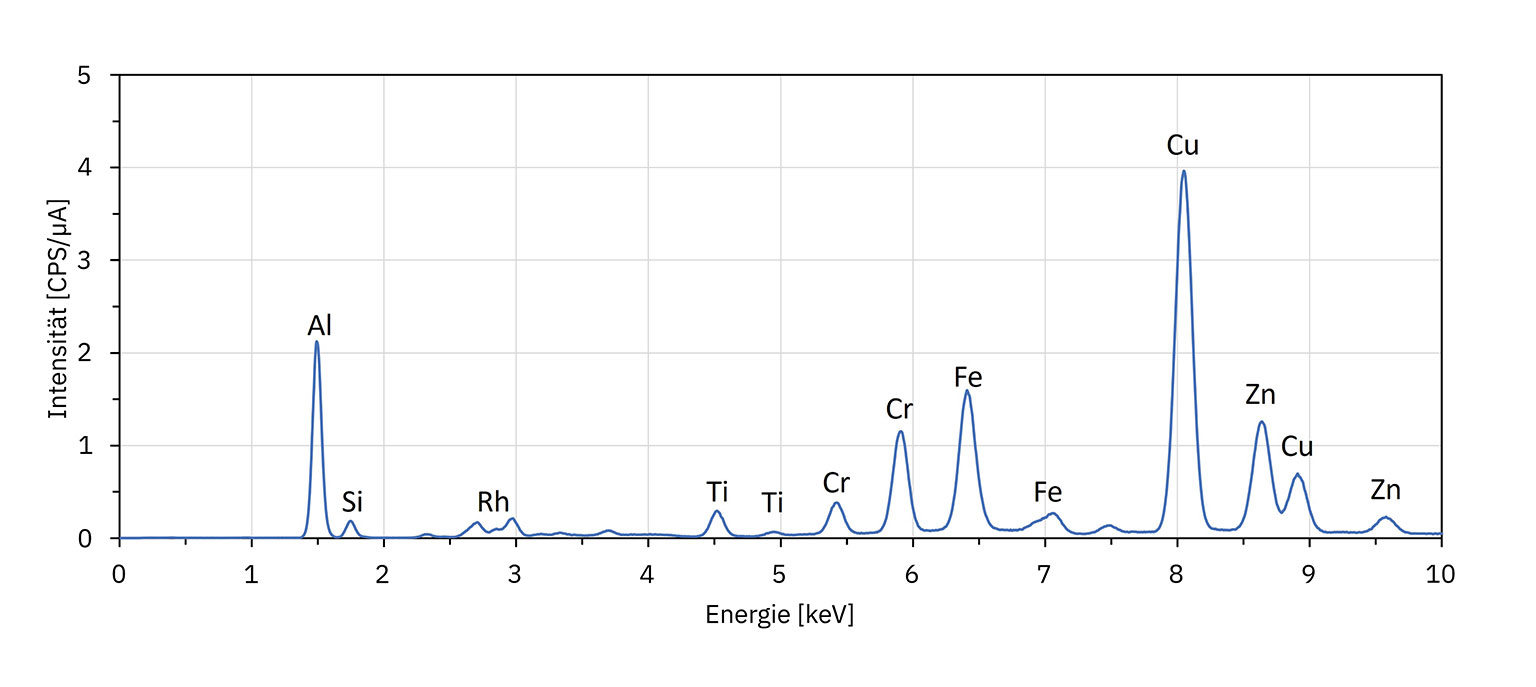
Element |
Al |
Si |
Cu |
Fe |
Zn |
Mn |
Mg |
Ti |
Cr |
Zertifikat |
85,02 |
6,90 |
3,90 |
1,01 |
0,99 |
0,83 |
0,42 |
0,29 |
0,26 |
EDX |
85,31 |
7,99 |
2,72 |
0,94 |
0,87 |
0,81 |
0,00 |
0,32 |
0,29 |
Beispiel 2: Zusammensetzung des Bads und Abwassers
Die korrekte Zusammensetzung des Galvanikbads ist wichtig für ein gutes Beschichtungsergebnis. Bei Verwendung einer unlöslichen Anode muss das Grundmaterial der Beschichtung in der richtigen Konzentration in Form von löslichen Salzen beigemischt werden. Daneben wird das Bad im Prozess auch verunreinigt, zum Beispiel durch anhaftende Flüssigkeit aus anderen Produktionsschritten. Daher müssen regelmäßig Proben entnommen und auf ihre chemische Zusammensetzung untersucht werden.
Das Bad enthält dabei neben konzentrierten Säuren in der Regel eine Vielzahl giftiger und umweltschädlicher Substanzen. Daher ist auch eine Kontrolle des Abwassers erforderlich. Im Gegensatz zum Galvanikbad selbst müssen hier kleinste Konzentrationen im ppm-Bereich zuverlässig bestimmt werden. Tabelle 3 zeigt die maximal erlaubten Konzentrationen für Schwermetalle im Abwasser eines Galvanikbetriebs nach deutscher Abwasserverordnung.[2]
Flüssige Proben können mittels EDX ohne weitere Aufbereitung in einer Zelle aus Kunststoff gemessen werden. Verschiedene Materialien sind erhältlich, je nach geforderter chemischer Beständigkeit. Der Boden besteht aus einer dünnen Polymerfolie, um die Röntgenstrahlung so wenig wie möglich abzuschwächen. Die Detektionsgrenzen liegen je nach Messparametern und Qualität der Kalibration typischerweise zwischen 0,1 und 5 ppm.
Element |
Probe 1 |
Probe 2 |
Probe 3 |
|
Au |
0,05 |
0,03 |
0,03 |
|
Ni |
2,24 |
0,53 |
0,56 |
|
Cu |
14,00 |
13,50 |
31,60 |
|
Fe |
∞ |
Beispiel 3: Schichtdicke
EDX ist eine Methode der Oberflächenanalytik. Die Eindringtiefe der Röntgenstrahlung liegt je nach Material unterhalb von 100 µm. Ist die Probendicke unterhalb der Eindringtiefe, so hängt die Stärke einer Linie neben der Konzentration des entsprechenden Elements auch von der Schichtdicke ab. Daher kann bei bekannter Zusammensetzung einer Beschichtung aus dem Spektrum auf die Schichtdicke zurückgerechnet werden – auch ohne Kalibration.
Auch die Analyse von Mehrschichtsystemen ist möglich, sofern alle Schichten durchstrahlt werden können. Durch eine spezielle Methode („Background Fundamental Parameters“-Methode) ist sogar die präzise Bestimmung von Schichtdicken auf unregelmäßig geformten Bauteilen, wie z. B. Schrauben, möglich.
Ein Beispiel ist in Abbildung 5 gezeigt. Die Eisen- und Kupferlinien werden in diesem System durch die darüberliegende Nickelschicht abgeschwächt. In Probe 3 ist die Kupferschicht zwar fast doppelt so dick wie in Probe 2, der Intensitätszugewinn fällt aber durch diese Abschwächung gering aus. In Probe 1 ist die Nickelschicht mehr als viermal so dick wie in Proben 2 und 3. Die Intensitäten der Eisen- und Kupferlinien sind dadurch deutlich geringer, obwohl die Kupferschicht genauso dick ist wie in Probe 2.
Die Dicke der oberen Nickel- und Goldschicht wirkt sich wie erwartet direkt auf die Intensitäten der Nickel- und Goldlinie aus. Die oberste Goldschicht ist in allen Proben zu dünn, um die Nickellinien nennenswert abzuschwächen.
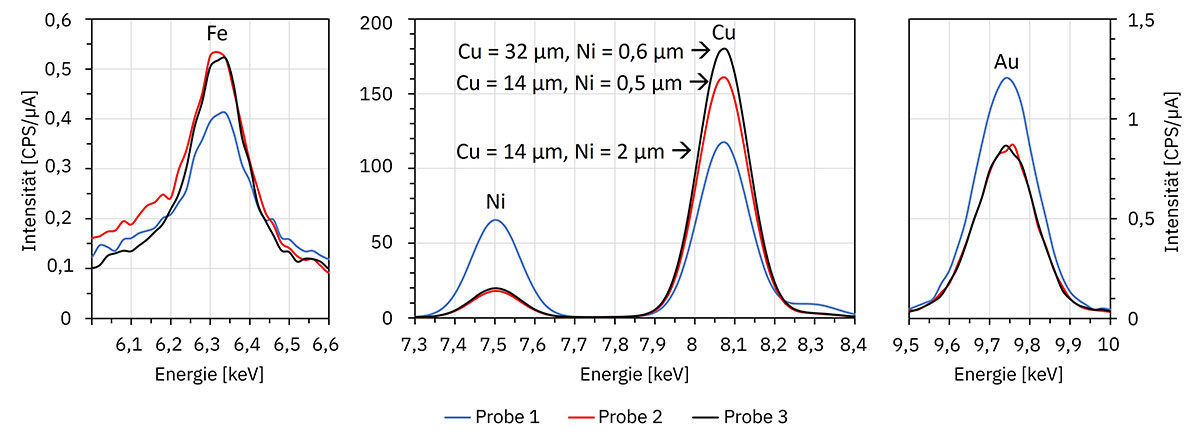
Element |
As |
Pb |
Cd |
Cl |
Cr |
Cu |
Ni |
Ag |
Sn |
Zn |
max. ppm |
0,1 |
0,5 |
0,2 |
0,5 |
0,5 |
0,5 |
0,5 |
0,1 |
2 |
2 |
PCEDX-Navi-Software
Die Möglichkeiten und Applikationen zur EDX-Analyse erscheinen zunächst vielfältig und komplex und tatsächlich gibt es bei der Erstellung einer neuen EDX-Analysemethode viel zu bedenken. In der Praxis ermöglicht die PCEDX-Navi-Software eine einfache Bedienung (Abbildung 6). Hier können die vorgefertigten Methoden aufgerufen werden und die Handgriffe sind intuitiv. Der Messfleck kann über ein Kamerabild kontrolliert und optimiert werden.
In jeder Methode können auch Qualitätskriterien (pass/fail) für die jeweilige Probenart hinterlegt werden. So erhält der Anwender eine unmittelbare Rückmeldung, ob die Probe in Ordnung ist (Abbildung 7). Die Resultate können anschließend als Bericht mit einer zuvor in Microsoft Excel erstellten Vorlage exportiert werden.
Viele analytische Fragestellungen der Galvanikindustrie lassen sich mit EDX-Spektroskopie beantworten. Mit einem Gerät können so flüssige oder feste Proben zerstörungsfrei und mit einfachen Handgriffen gemessen werden. Dies spart Platz im Labor, schont das Budget und verkürzt Einarbeitungszeiten. Im Gegensatz zu Methoden wie der Atomabsorptionsspektroskopie können flüssige Proben dabei unverdünnt gemessen und auch Halogene bestimmt werden. Bei festen Proben können sowohl die Zusammensetzung als auch die Schichtdicken bestimmt werden, sodass hier keine zusätzlichen Geräte beschafft werden müssen.
Referenzen/Weitere Informationen
- https://www.zvo.org/verband (accessed on 14/07/2022)
- Annex 40 Waste Water Ordinance (AbwV)