Ein „Nervensystem“ für Infrastrukturbauwerke
Entwicklung und Prüfung verteilter faseroptischer Sensoren und anderer diagnostischer Lösungen
Kamil Badura, Tomasz Howiacki,
SHM System/Nerve-Sensors
Moderne Gesellschaften benötigen eine intelligente Infrastruktur, die mit Frühwarnsystemen ausgestattet und in der Lage ist, Gefahren zu erkennen. Obwohl Gebäude und Infrastrukturen für eine lange Nutzungsdauer gebaut werden, kommt es weltweit häufig zu Einstürzen. Das Diagnostizieren von Ingenieur- und geotechnischen Bauwerken ist daher unerlässlich, um Schäden vorzubeugen und Menschenleben zu retten. Einer der vielversprechendsten Ansätze ist die vollständige Integration von monolithischen faseroptischen Sensoren zur kontinuierlichen Überwachung der Dehnung, Verschiebung, Temperatur und Vibration über die gesamte Länge eines Bauwerks – vom Millimeter- bis in den Kilometerbereich.
Der Einsturz der Autobahnbrücke Ponte Morandi in Genua 2018 machte als scheinbarer Einzelfall weltweit Schlagzeilen. Tatsächlich ist der Einsturz von Infrastrukturbauwerken jedoch gar nicht so selten. Jedes Jahr stürzen zahlreiche Gebäude und Brücken ein – viele davon, weil die tragende Struktur altersbedingt versagt. Und nicht alle Gebäude werden gleich gebaut. Moderne Infrastruktur wird in der Regel mit ungewöhnlichen Formen unter Verwendung neuer Materialien und innovativer Lösungen geplant. Andererseits erfordert alternde Infrastruktur eine fachgerechte Instandhaltung, um ein angemessenes Maß an Sicherheit zu gewährleisten. Kenntnisse des mechanischen und thermischen Verhaltens eines Bauwerks unter normalen Betriebsbedingungen sind daher unerlässlich, um den technischen Zustand bewerten und optimale Entscheidungen treffen zu können.
Die Verantwortung für die umgebende Infrastruktur führt zur Suche nach effektiven Lösungen, die einen gesamtgesellschaftlichen Nutzen haben können. Zunächst einmal kann eine ordnungsgemäße Überwachung dabei helfen, das Versagen oder den Einsturz sicherheitskritischer Bauwerke zu verhindern, was unmittelbar zum Schutz von Leib und Leben beiträgt. Zweitens bringt sie wirtschaftliche, ökologische und soziale Vorteile. Besonders zu beachten ist auch, dass das Wissen, das aus den realen Bedingungen vor Ort gewonnen wird, zu einem besseren Verständnis der in der Natur und im Ingenieurbau auftretenden Phänomene beiträgt und somit hilft, unsere theoretischen Modelle zu verbessern und künftige Lösungen zu optimieren.
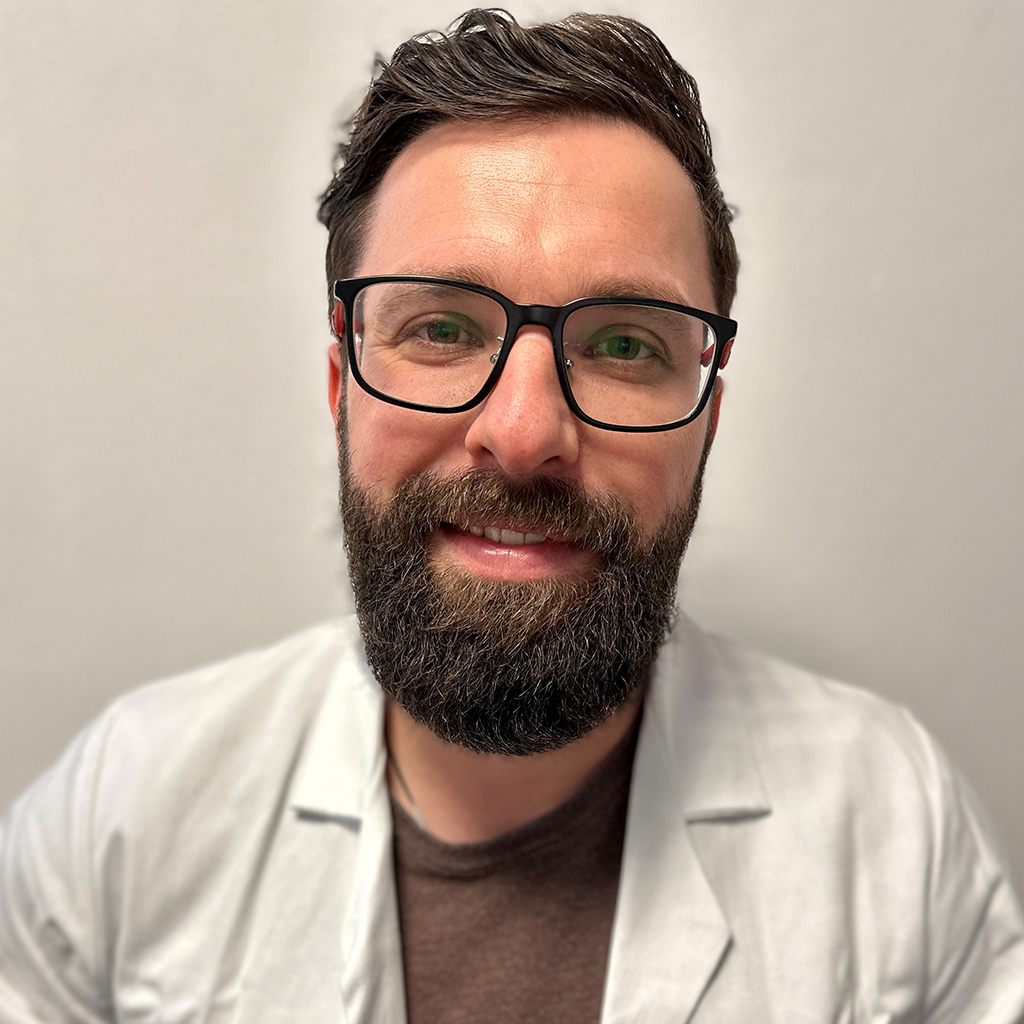
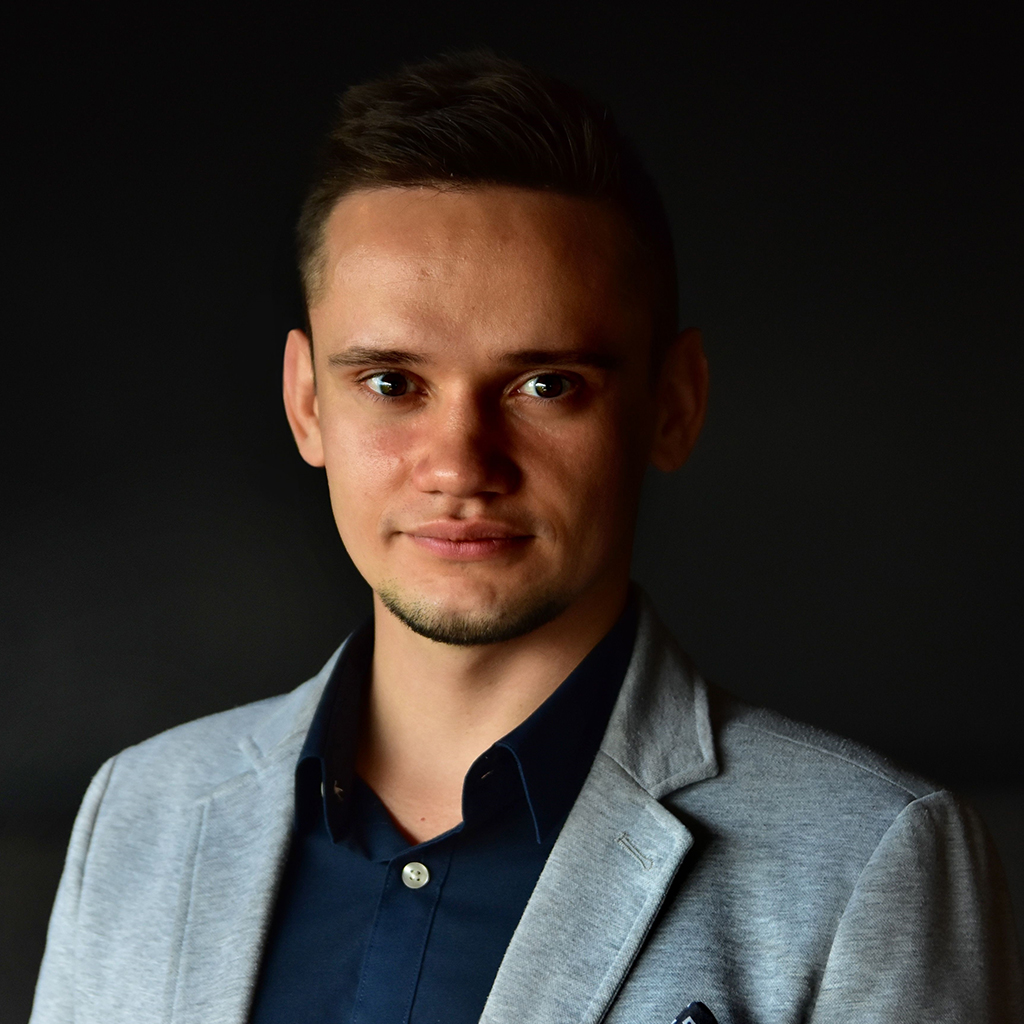
Monolithische faseroptische Sensoren – ein „Nervensystem“ für Bauwerke
Angesichts der zahlreichen Messtechnologien, die auf dem Markt verfügbar sind, herrscht eine ständige Suche nach der optimalen Lösung für die Diagnose von Ingenieur- und geotechnischen Bauwerken. Einer der vielversprechendsten Ansätze ist die vollständige Integration von monolithischen faseroptischen Sensoren zur kontinuierlichen Überwachung der Dehnung, Verschiebung [1], Temperatur und Vibration über die gesamte Länge [2] eines Bauwerks – vom Millimeter- bis in den Kilometerbereich. Anstatt eines einzigen lokalen Messwertes direkt am Messgerät erhalten wir ein kontinuierliches Profil der gemessenen Größen, sodass Anomalien oder lokale Ereignisse wie z. B. Rissbildung [3], Spannungskonzentrationen oder andere Schäden festgestellt werden können.
Trotz der unbestreitbaren Vorteile der DFOS-Technologie (Distributed Fiber Optic Sensing) ist diese keine „Plug-and-play“-Lösung. Es gibt zahlreiche Aspekte, die vor der Messung sorgfältig geplant und berücksichtigt werden müssen. Dazu gehören die Art der Sensoren und deren Parameter wie z. B. Durchmesser, Elastizitätsmodul, äußere Oberfläche oder internes Design. Innerhalb von SHM System befasst sich die Abteilung „Nerve-Sensors“ mit der Planung, Entwicklung und Erforschung von weltweit einzigartigen monolithischen DFOS-Sensoren.
Erste Marktforschung kam 2015 zu dem Ergebnis, dass es keine Alternativen zu geschichteten Sensorkabeln für reale Anwendungen gab. Diese Lösung kannte man aus der Telekommunikation, wo faseroptische Sensoren durch mehrere Schichten geschützt werden. Aus messtechnischer Sicht war ihr Einsatz jedoch durch mehrere Nachteile eingeschränkt. Erstens führte die Verwendung von Kunststoff- und Stahlkomponenten mit einer geringen Elastizität zu einer sehr schnellen Zerstörung der Kabel. Zweitens störten die Zwischenschichten durch den Gleiteffekt den Mechanismus der Dehnungsübertragung. Schließlich bot die glatte Außenfläche keinen ausreichenden Verbund an das umgebende Material.
Eine zukunftsweisende Innovation nach dem Vorbild des menschlichen Körpers
Es gab keine Lösung auf dem Markt, die eigens für die Überwachung von Ingenieur- und geotechnischen Bauwerken konzipiert war. Um diese Lücke zu schließen und die bestehenden Einschränkungen zu überwinden, wurde die Nerve-Sensors-Produktfamilie entwickelt. Diese neuen Sensoren bestehen aus einem monolithischen Kern ohne Schichten und ermöglichen somit besonders genaue Dehnungsmessungen. Komponenten aus Kunststoff und Stahl wurden durch hochelastische Verbundmaterialien ersetzt. Ein äußeres Geflecht verbessert die Qualität des Verbunds zwischen dem Sensor und dem umgebenden Material, z. B. Beton oder Erdboden. Monolithische Sensoren sind so konzipiert, dass sie – ähnlich wie ein Nervensystem – in ein Bauwerk integriert werden können [4] – daher der Name der Produktfamilie.
Kalibrierung für Effektivität und Genauigkeit mit Prüfmaschinen von Shimadzu
Monolithische Sensoren heben Structural Health Monitoring (SHM) auf eine vollkommen neue Stufe. Um jeden Zweifel an ihrer Effektivität und Genauigkeit auszuräumen, war jedoch eine präzise und strenge Laborprüfung nötig. Dazu wurde das Labor von SHM System mit zwei Prüfmaschinen von Shimadzu ausgestattet: der AGS-50kNX und der AGX-V-300kN (Abbildung 1). Beide werden für die präzise mechanische Prüfung verschiedener Arten von monolithischen Sensoren eingesetzt, z. B. dem steifen und robusten EpsilonRebar oder dem flexiblen und vielseitigen EpsilonSensor (Abbildung 2). Die wichtigsten Spezifikationen, die analysiert werden müssen, sind die Genauigkeit der Dehnung und der maximale Messbereich der Dehnung. Dank des speziellen Kerns aus Verbundstoff verfügt der EpsilonSensor auf dem gesamten Markt über den größten Messbereich von bis zu 4 % (Abbildung 3) – das entspricht dem Vierfachen des typischen Bereichs von Schichtkabeln. Dies eröffnet neue Möglichkeiten für die Zustandsanalyse von Bauwerken, einschließlich der Messung lokaler Riss- und Bruchbildung, die mit konkurrierenden Lösungen nicht erreichbar ist.
Die Prüfmaschinen von Shimadzu sind kontinuierlich im Einsatz – nicht nur für die statistische Analyse einer großen Anzahl an Proben, sondern auch für die Entwicklung und Prüfung neuer, verbesserter Lösungen für die ständig wachsende Nerve-Sensors-Produktfamilie, die spezifische Marktbedürfnisse erfüllen. Materialien, Querschnitte oder äußere Oberflächenmerkmale verändern sich mit der Zeit. So verbessert der Zusatz von Graphit die Wärmeleitfähigkeit des Temperatursensors und der rechteckige Querschnitt erleichtert die Montage auf ebenen Flächen. Dabei ist jedes Mal eine angemessene Prüfung erforderlich.

Die Integration neuer Sensortechnologie in bestehende Bauwerke
In der Praxis wird das Verfahren des Distributed Sensing durch punktuelle diagnostische Lösungen ergänzt. Auch diese werden im Labor von SHM System entwickelt und geprüft. Zwei davon stellen wir in diesem Abschnitt genauer vor. Die erste Lösung ist der „Plastic Deformation Sensor“ (PDS) – der weltweit erste und einzige Sensor, der in der Lage ist, das sogenannte Fließen von Stahl ohne Kenntnis der Materialeigenschaften, des ursprünglichen Spannungs-Dehnungs-Zustands und des tatsächlichen technischen Zustands zu erkennen. Dieser Sensor eignet sich nicht nur für die Diagnose von Stahlstrukturen, sondern auch für die Erkennung der Ausfallgefährdung anderer Baustoffe wie z. B. Beton. Der Sensor kann auf Grundlage von verschiedenen Messtechnologien entwickelt werden, z. B. faseroptischen Sensoren (Abbildung 4), Dehnungsmessstreifen (Abbildung 5) oder Schwingsaitenaufnehmern (Abbildung 6). Er lässt sich daher problemlos in bestehende Überwachungssysteme integrieren. Dank des speziellen Berechnungsalgorithmus eignet er sich ausgezeichnet für die Diagnose neuer und bestehender, alternder Infrastruktur mit unbekanntem Deformationszustand und fehlender Dokumentation.
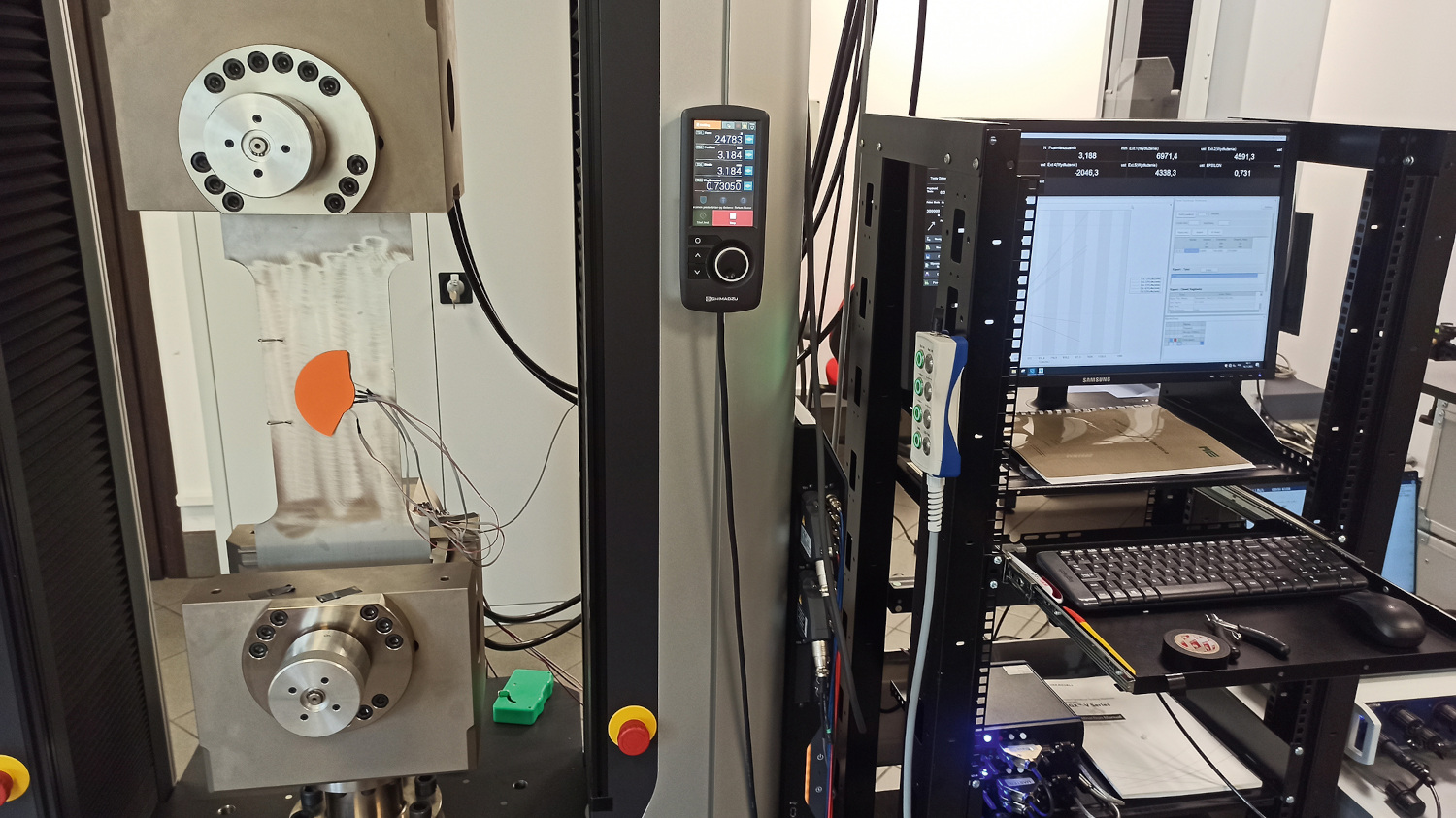
Die zweite einzigartige Lösung verwendet Faser-Bragg-Gitter (FBG), eines der am häufigsten eingesetzten punktuellen faseroptischen Messgeräte. Leider haben herkömmliche FBG einen begrenzten Dehnungsbereich und eignen sich nur für die Messung gleichförmiger Materialien, normalerweise innerhalb ihres elastischen Verhaltens. Bei starken Verformungen inhomogener Baustoffe wie z. B. Beton (lokaler Einfluss von Zuschlägen oder Rissen), Verbundtextilien (Störung durch senkrecht verlaufende Fasern) oder einfach Stahl im plastifizierten Zustand spalten herkömmliche FBG das Spektrum auf, sodass eine weitere Messung unmöglich ist. Der neue FBG-Sensor, der von den Spezialisten von SHM System entwickelt wurde, überwindet diese Einschränkungen und ermöglicht es, den Messbereich und somit die möglichen Anwendungen erheblich zu erweitern.
Der neue „Plastic Deformation Sensor“ und der neue FBG-Sensor werden auf unterschiedlichen Materialproben installiert und anschließend mit den Prüfmaschinen von Shimadzu geprüft. Die durch das Messystem erfassten Daten werden mit den geprüften Technologien synchronisiert und liefern verlässliche Referenzdaten. So wird der aus den rohen Dehnungsdaten berechnete PDS-Koeffizient mit den von der Shimadzu- Prüfmaschine ermittelten Kraftwerten verglichen (Abbildung 7), um die Effektivität des PDS bei der Bestimmung der Fließzeit zu beurteilen.
Vor einigen Jahren noch ein Traum – heute eine lebensrettende Innovation
An dieser Stelle sei noch einmal betont, dass das Versagen von Ingenieur- und geotechnischen Bauwerken nicht nur finanzielle, soziale und ökologische Folgen hat, sondern auch Leib und Leben von Menschen bedroht. Um Menschenleben zu retten, hat das Team von SHM System und Nerve-Sensors den Kreis geschlossen und sich vom menschlichen Nervensystem als perfektesm Frühwarnsystem inspirieren lassen. Das menschliche Nervensystem diente als unübertroffenes Modell für die Entwicklung eines Systems zur Diagnose von Ingenieur- und geotechnischen Bauwerken. Die linearen Verbundsensoren werden vollständig in das Bauwerk integriert und dienen sozusagen als „Nerven“, die Gefahren erkennen, während der Datenlogger als das „Gehirn“ die Daten verarbeitet, visuell darstellt und interpretiert. Was noch vor wenigen Jahren ein Traum war, ist heute schon in Hunderten von Brücken [5] und anderen Infrastrukturbauwerken weltweit Realität und rettet nicht nur Bauwerke, sondern vor allem auch Menschenleben.
[1] Bednarski, Ł., Sieńko, R., Grygierek, M., Howiacki, T. (2021). New Distributed Fibre Optic 3D Sensor with Thermal Self-Compensation System: Design, Research and Field Proof Application Inside Geotechnical Structure. Sensors. 21: 5089. https://doi.org/10.3390/s21155089.
[2] Piątek, B., Howiacki, T., Kulpa, M., Siwowski, T., Sieńko, R., Bednarski, Ł. (2023). Strain, crack, stress and shape diagnostics of new and existing post-tensioned structures through distributed fibre optic sensors. Measurement. 221: 113480. https://doi.org/10.1016/j.measurement.2023.113480.
[3] Howiacki, T., Sieńko, R., Bednarski, Ł., Zuziak, K. (2023). Crack Shape Coefficient: Comparison between Different DFOS Tools Embedded for Crack Monitoring in Concrete. Sensors. 23: 566. https://doi.org/10.3390/s23020566.
[4] Bednarski, Ł., Sieńko, R., Howiacki, T., Zuziak, K. (2022). The Smart Nervous System for Cracked Concrete Structures: Theory, Design, Research, and Field Proof of Monolithic DFOS-Based Sensors. Sensors. 22: 8713. https://doi.org/10.3390/s22228713.
[5] Howiacki, T., Sieńko, R., Bednarski, Ł., Zuziak, K. (2023). Structural monitoring of concrete, steel, and composite bridges in Poland with distributed fibre optic sensors. Structure and Infrastructure Engineering. 1–17. https://doi.org/10.1080/15732479.2023.2230558.