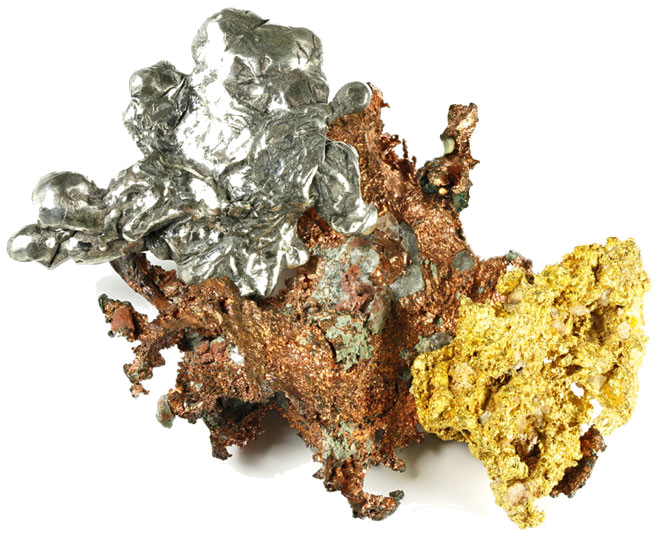
Rust protection with X-rays
The EDX-7200 as a Swiss Army knife in the quality control of electroplating
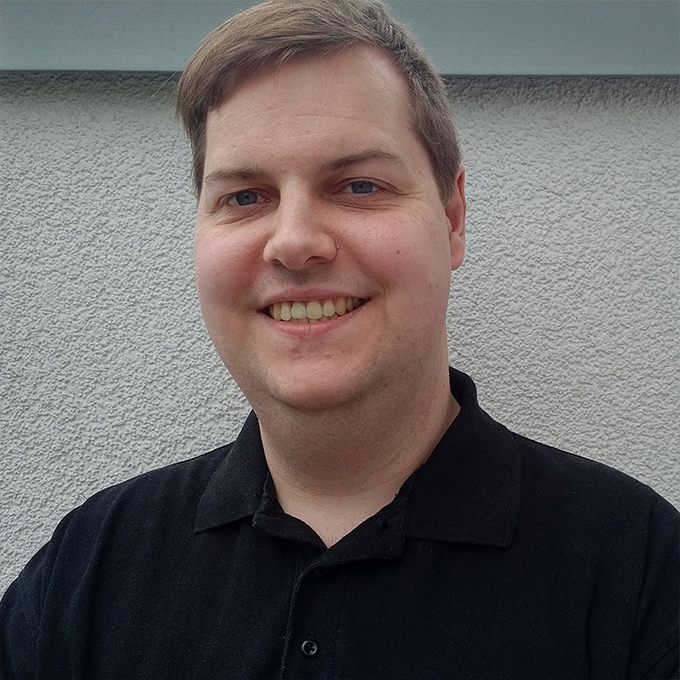
Dr. Benjamin Thomas, Shimadzu Europa GmbH
Electroplated products have become an essential part of our everyday lives, from rhodium-plated wedding rings to chrome-plated motorbike exhausts. Many of the analytical questions related to electroplating (from the composition of the electroplating bath to the thickness of the applied coating) can be answered in a non-destructive manner using energy-dispersive X-ray fluorescence spectroscopy. Shimadzu’s EDX-7200 is a high-speed spectroscopic device that sensitively and precisely performs in a multitude of electroplating applications.
Energy-dispersive X–ray fluorescence (ED-XRF) is a non-destructive analytical technique that can be used to analyze the elemental composition of a sample. During this process, the sample is exposed to X-radiation, better known as X-rays. The energy distribution and flux density of the X-ray photons can be optimized for the particular analysis by adjusting voltage and current at the X-ray tube and by the interposition of absorption filters.
The principle is best described using Bohr’s atomic model (Figure 1). The irradiation knocks electrons out of the atomic orbitals (“shells”) of the elements contained in the sample (1). This creates a so-called “hole” (2). The energy required for this excitation depends on the atomic number of the element in question. The excited atom now returns to the energetic ground state by filling the resulting “hole” with an electron from a higher shell (3).
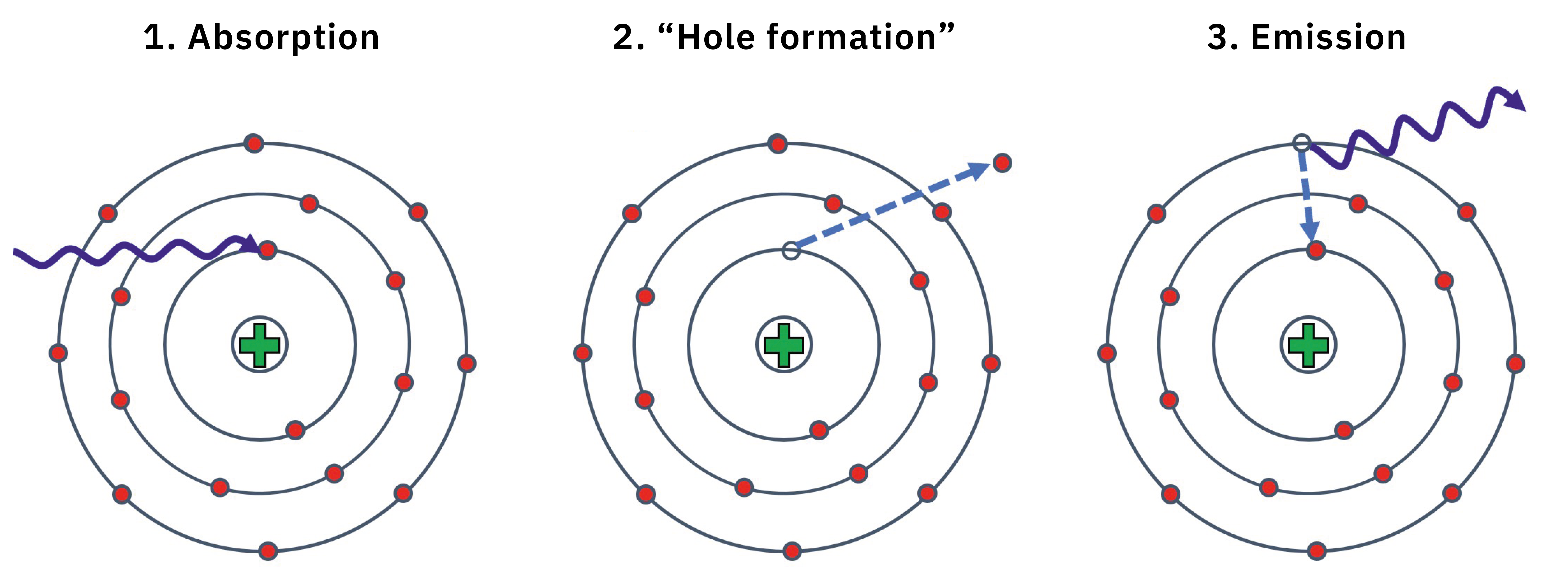
Figure 1: X-ray fluorescence explained on the Bohr atomic model
According to the principle of the conservation of energy, excess energy must be emitted in the form of light. The energy difference between two shells (and therefore the energy of the emitted photon in kiloelectronvolts (keV)) can be calculated quantum-mechanically and is characteristic for each element. This means the elemental composition of the sample can be calculated from the spectrum and, if the composition of each layer is known, the layer thicknesses can also be calculated. Depending on the composition and density, the X-rays penetrate into the sample up to 100 µm.
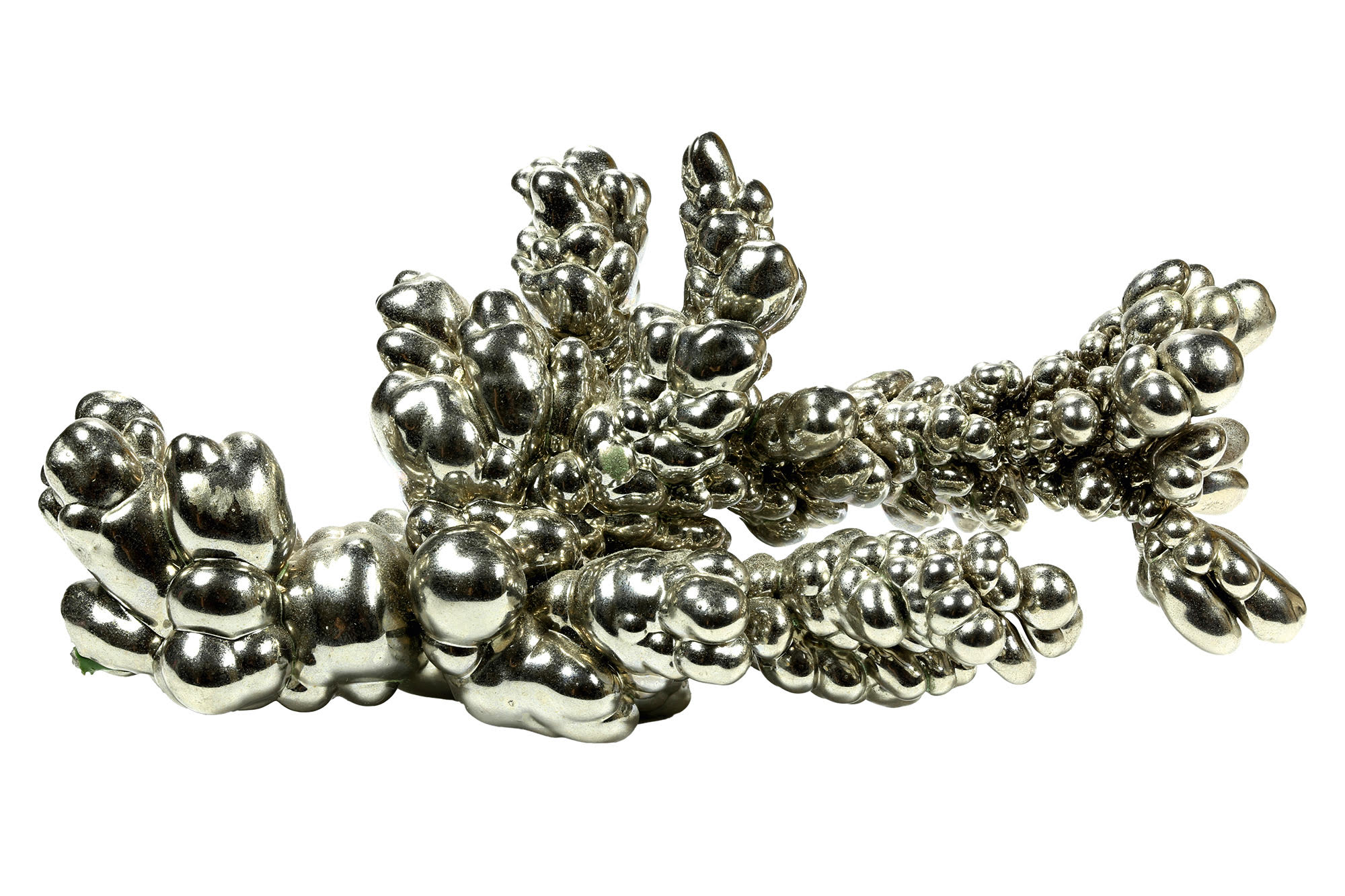
Corrosion
A lot of everyday objects as well as building materials are made of metallic substances. Most metals exist in nature in the form of ores, i.e. in chemical combination with oxygen (oxides) or oxygen and carbon (carbonates). The resulting metals are correspondingly susceptible to reactions with oxygen or acids and, if left in contact with air and moisture unprotected, return to their original state in the long term – i.e., they corrode.
Corrosion is an electrochemical process where water acts as an electrolyte. During the process, the metal releases electrons to oxygen dissolved in the water (Figure 2). Negatively charged hydroxide anions and positively charged metal cations dissolved in the water droplet are formed. This, in turn, produces insoluble metal oxide, which is deposited on the surface of the metal body or washed off with the water droplet.
While some metals, such as aluminum, form a continuous, stable oxide layer upon contact with air and, as a result, protect against further corrosion, the oxides of other metals, such as iron, are deposited loosely and are permeable to water. This is how the corrosion literally “eats” its way through the metal body until the structure of the corresponding component collapses. Acids as well as contact with other metals (“bimetallic corrosion”) facilitate this process.
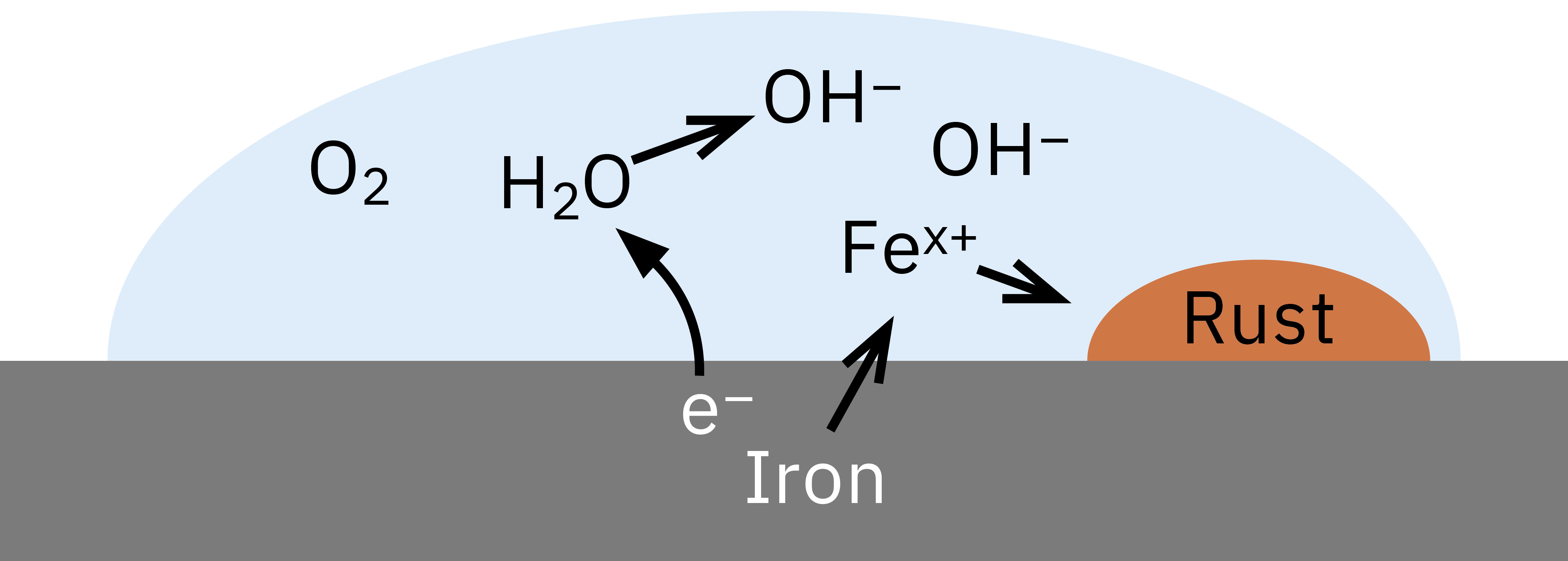
Figure 2: Electrochemical reactions during rust formation
Corrosion protection
There are different approaches to corrosion protection (Table 1). In most cases, corrosion protection is achieved by a coating with other metals, resin or a combination of both (“duplex system”). For example, you can go to the hardware store and find “hot-dip galvanized” screws, i.e. coated in a molten zinc; in the kitchen, you can find galvanized gold-plated cutlery. Even a wedding ring made of white gold is usually electroplated rhodium, i.e. protected from corrosion by a thin rhodium coating.
Each technique has its own advantages and disadvantages. Protection through coating with a precious metal (e.g. gold plating) is usually long-lasting, as the protective layer is chemically stable. However, in the case of scratches or faulty coating, this could actually accelerate the corrosion compared to the unprotected workpiece. A base metal coating (e.g. zinc plating) provides indirect protection in the event of scratches, as it is the coating that dissolves instead of the base material. However, it is less durable as a result.
Principle |
Mode of action |
Advantage |
Disadvantage |
Example |
Coating with precious metal |
Protective layer not prone to corrosion |
Longevity |
Accelerated corrosion in case of damage |
Vitrification, chrome plating |
Base metal coating |
Protective layer acts as sacrificial anode |
Protection even in case of damage |
Protective layer dissolves slowly |
Galvanizing, sacrificial anodes on the hull of the ship |
Coating with plastic |
Protective layer not prone to corrosion |
No bimetal corrosion |
Low mechanical stability |
Teflon coating, protective varnish |
Application of external current |
Continuously “resupply” lost electrons |
Wear-free |
Only feasible on a large scale |
Bridges, pipelines, superstructures |
Electroplating processes
During electroplating processes, an electrically conductive workpiece is coated by an electrochemical deposition of metal from an electrolyte solution. This means that both metals are immersed in a conductive bath, and a direct current is applied (Figure 3). Here, the workpiece to be coated serves as the cathode and the original material of the coating as the anode. Due to the current flow, the original material is gradually degraded and enters into solution in the form of ions. Alternatively, an insoluble stainless steel anode is often used in engineering, and the coating material is supplied in the form of soluble salts. In both cases, the ions dissolved in the electroplating bath are reduced again by the current applied to the workpiece to form the metal, which is deposited on the workpiece in layers.
The large-scale application of these processes is very complex. The chemical composition of the bath must be closely monitored, including both the current strength and coating time. In practice, several different layers are often necessary to achieve mechanically and chemically stable and durable corrosion protection. The following three examples demonstrate how EDX spectroscopy can be used to quickly and efficiently check original materials, intermediates and end products.
Example 1: Composition of the base alloy
The possible coatings, required parameters and pretreatment depend on the material of the workpiece to be coated. Stainless steel, for example, can be polished to a mirror finish and chrome-plated directly, while other types of steel must first be copper-plated and nickel-plated to create a base for the final chrome layer.
EDX spectroscopy makes it easy to identify the composition of an alloy. A measurement time of 30 seconds is often sufficient, depending on the number of expected elements. A qualitative/quantitative result can also be determined without calibration. Since the position of the element-specific lines is known, all measured lines can be assigned automatically. A distribution is then issued, based on the intensity ratios.
Since chemical interactions among alloying elements can affect the quantum yields for each element, the precision of the result can be improved by calibration with appropriate standards. As a rule, qualitative/quantitative measurement is a first step. Based on the elements found, the sample is then measured again using a quantitative method to identify the exact composition (Table 2). Table 2 shows the results found without calibration for the aluminum-silicon alloy from Figure 4 in comparison with the certified values.
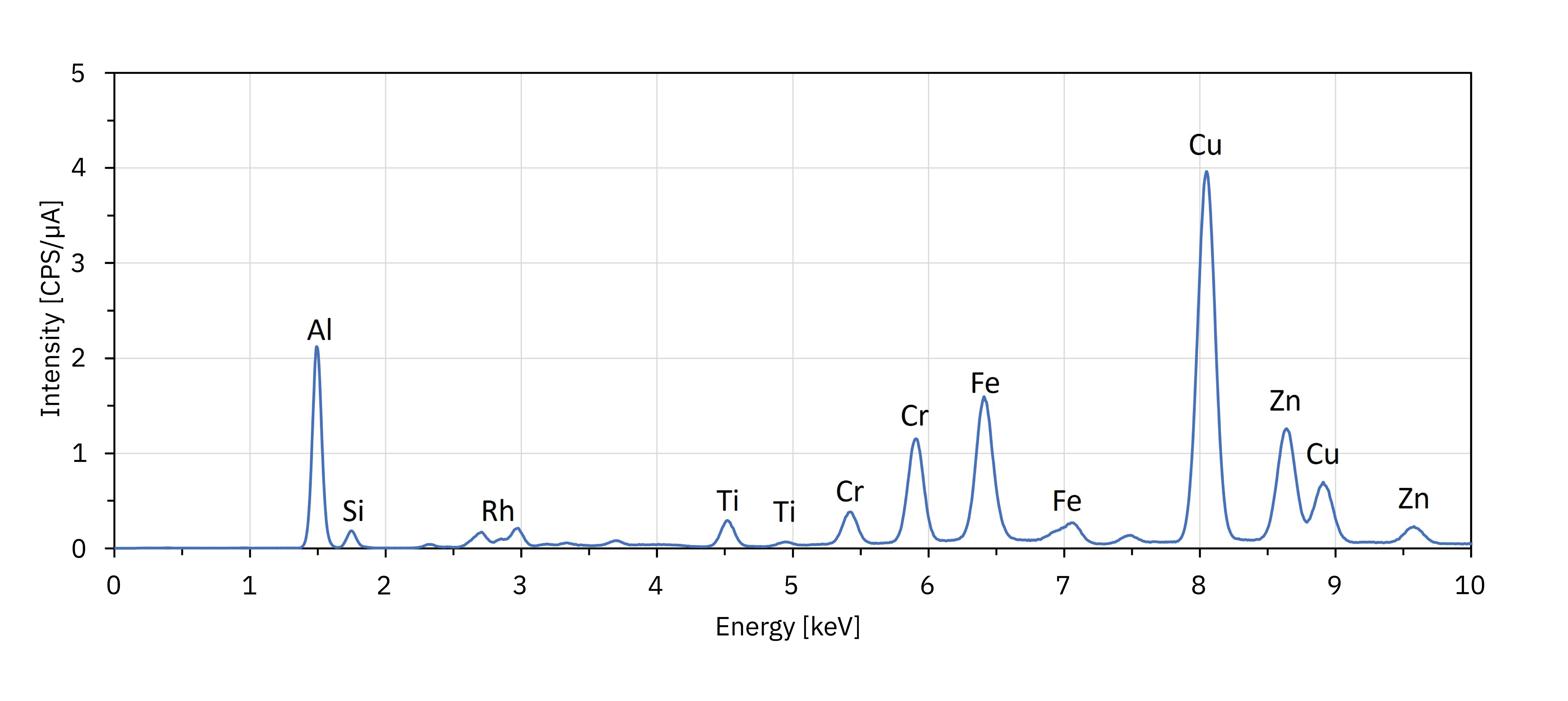
Element |
Al |
Si |
Cu |
Fe |
Zn |
Mn |
Mg |
Ti |
Cr |
Certificate |
85.02 |
6.90 |
3.90 |
1.01 |
0.99 |
0.83 |
0.42 |
0.29 |
0.26 |
EDX |
85.31 |
7.99 |
2.72 |
0.94 |
0.87 |
0.81 |
0.00 |
0.32 |
0.29 |
Example 2: Composition of the bath and wastewater
The correct composition of the plating bath is important for a good plating result. When using an insoluble anode, the base material must be added to the coating in the correct concentration in the form of soluble salts. In the process, the bath is also contaminated, for example by adhering liquid from other production steps. For this reason, samples must be taken regularly and analyzed for their chemical composition.
In addition to concentrated acids, the bath usually contains a large number of toxic and environmentally harmful substances. Therefore, it is also necessary to carefully analyze the wastewater. In contrast to the electroplating bath itself, the smallest concentrations in the ppm range must be reliably determined here. Table 3 shows the maximum permissible concentrations for heavy metals in the wastewater of an electroplating plant according to the German Waste Water Ordinance.[2]
Liquid samples can be easily measured by EDX, without further preparation in a plastic cell. Various cell materials are available, depending on the required chemical resistance. The bottom is made of a thin polymer film to weaken the X-rays as little as possible. Detection limits are typically between 0.1 and 5 ppm, depending on measurement parameters and the quality of calibration.
Element |
Sample 1 |
Sample 2 |
Sample 3 |
|
Au |
0.05 |
0.03 |
0.03 |
|
Ni |
2.24 |
0.53 |
0.56 |
|
Cu |
14.00 |
13.50 |
31.60 |
|
Fe |
∞ |
Example 3: Layer thickness
EDX is also a method of surface analysis. The depth of penetration of the X-rays is below 100 µm, depending on the material. If the sample thickness is below the depth of penetration, the thickness of a line depends not only on the concentration of the corresponding element but also on the layer thickness. This means that if the composition of a coating is known, the layer thickness can be calculated from the spectrum – even without calibration.
It is also possible to analyze multilayer systems, provided that all layers can be irradiated. Using a special method (“Background Fundamental Parameters”), it is even possible to precisely determine layer thicknesses on irregularly shaped components, such as screws.
One example is shown in Figure 5. In this system, the iron and copper lines are weakened by the overlying nickel layer. In Sample 3, the copper layer is almost twice as thick as in Sample 2, but the intensity gain is small due to this weakening. In Sample 1, the nickel layer is more than four times thicker than in Samples 2 and 3. As a result, the intensities of the iron and copper lines are significantly lower, although the copper layer is as thick as in Sample 2.
As expected, the thickness of the top nickel and gold layer directly affects the intensities of the nickel and gold lines. The top gold layer is too thin in all samples to significantly weaken the nickel lines.
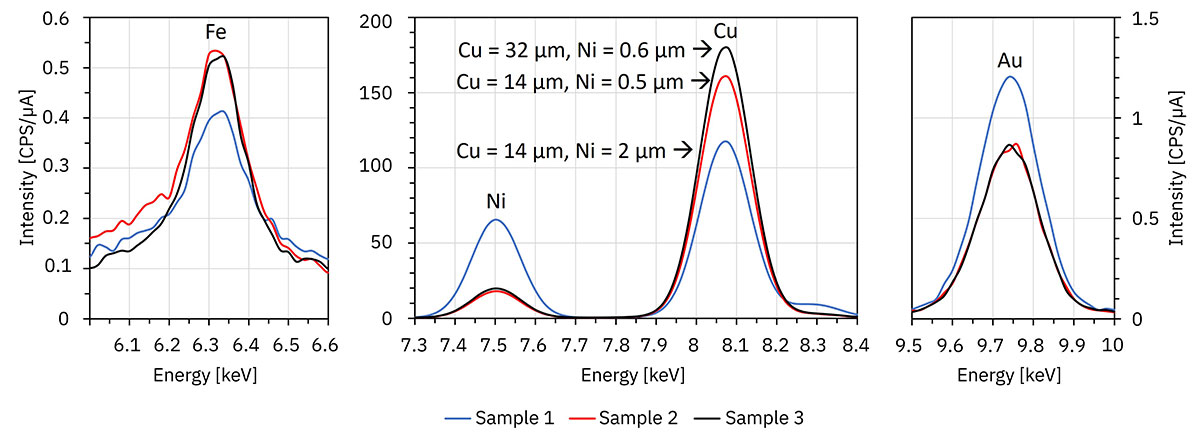
Element |
As |
Pb |
Cd |
Cl |
Cr |
Cu |
Ni |
Ag |
Sn |
Zn |
max. ppm |
0.1 |
0.5 |
0.2 |
0.5 |
0.5 |
0.5 |
0.5 |
0.1 |
2 |
2 |
PCEDX Navi software
At first glance, the possibilities and applications for EDX analysis may seem overly diverse and complex and there is indeed a lot to consider when creating a new EDX analysis method. In practice, however, Shimadzu’s PCEDX Navi software enables quite easy operation (Figure 6). Here, the pre-made methods can be called up and the handles are intuitive. The measuring spot can be controlled and optimized via a camera image.
Quality criteria (pass/fail) for the respective sample type can also be stored in each method. This provides the user with immediate feedback as to whether the sample is within the set parameters (Figure 7). The results can then be exported as a report using a template previously created in Microsoft Excel.
Many of the analytical questions facing the electroplating industry can be answered using EDX spectroscopy. With only one device, liquid or solid samples can be measured non-destructively, accurately and quickly. This saves space in the laboratory, is economical and shortens training times. In contrast to methods such as atomic absorption spectroscopy, liquid samples can be measured in an undiluted manner and halogens can also be determined. In the case of solid samples, both the composition and the layer thicknesses can be determined, all without the need for additional equipment. The EDX-7200 – Shimadzu’s Energy Dispersive X-ray Fluorescence Spectrometer –is an easy-to-use, multi-purpose device designed to meet the needs of the electroplating industry.
References/further information
- https://www.zvo.org/verband (accessed on 14/07/2022)
- Annex 40 Waste Water Ordinance (AbwV)