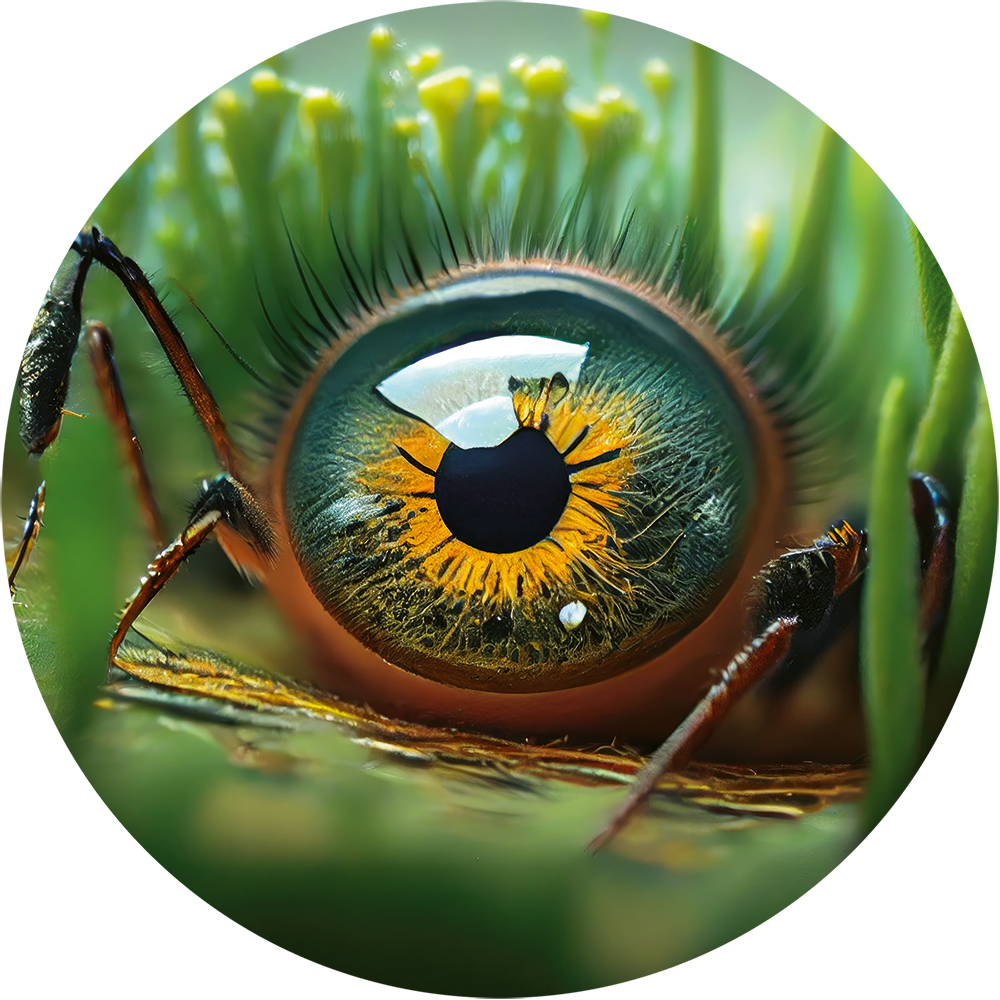
Pure performance: Saving time with ultra-fast preparative LC
How Syngenta is using UFPLC to extract and purify gram-scale by-products for regulatory tests
Louise Bacon, Cyprien Bone, Lorraine Ezra, Syngenta
Chemicals such as herbicides, fungicides, insecticides and seed treatments are widely used to maximize crop yields worldwide. Ensuring the efficacy and safety of products requires studying the formulations in detail, including even the most minor of components. In this article, we talk to Syngenta about how they’re using Shimadzu’s UFPLC systems to speed up the extraction and purification of gram quantities of by-products that are present in technical-grade active-ingredient material at levels below 1 %, so providing the material needed for regulatory tests and toxicity studies.
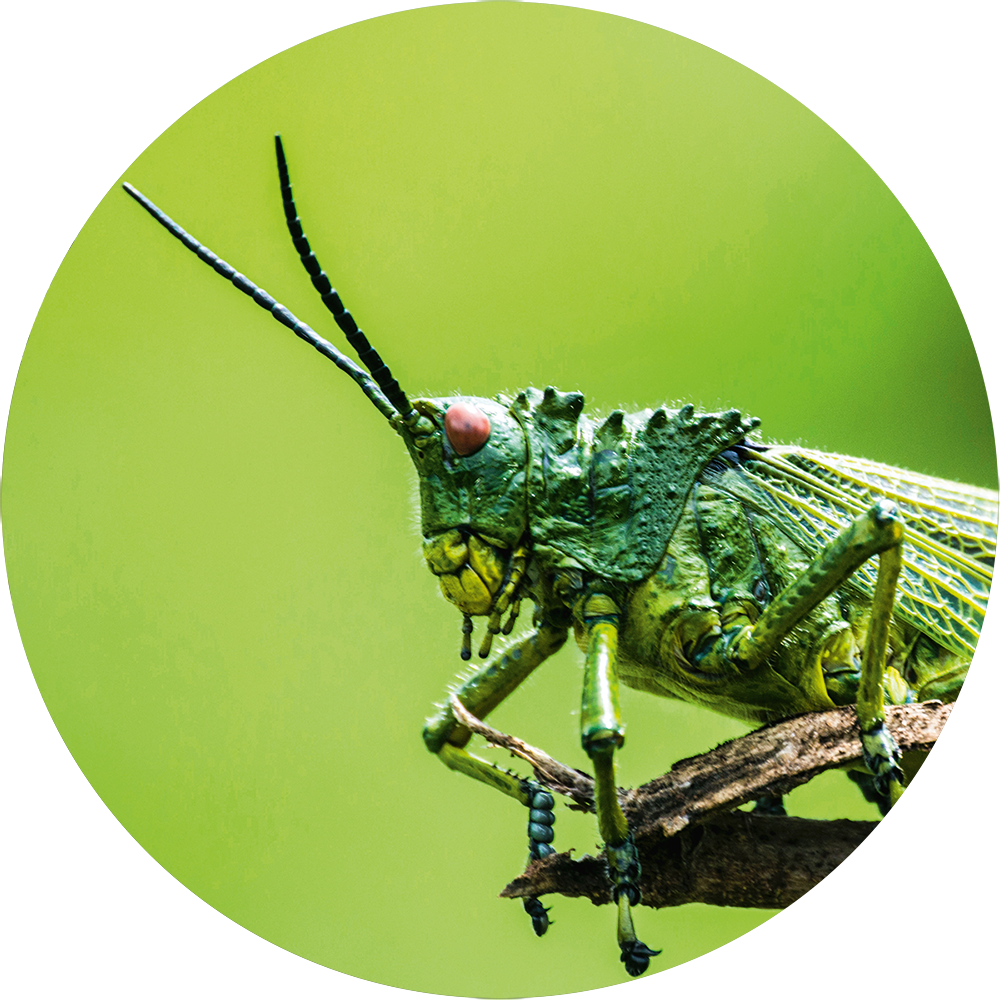
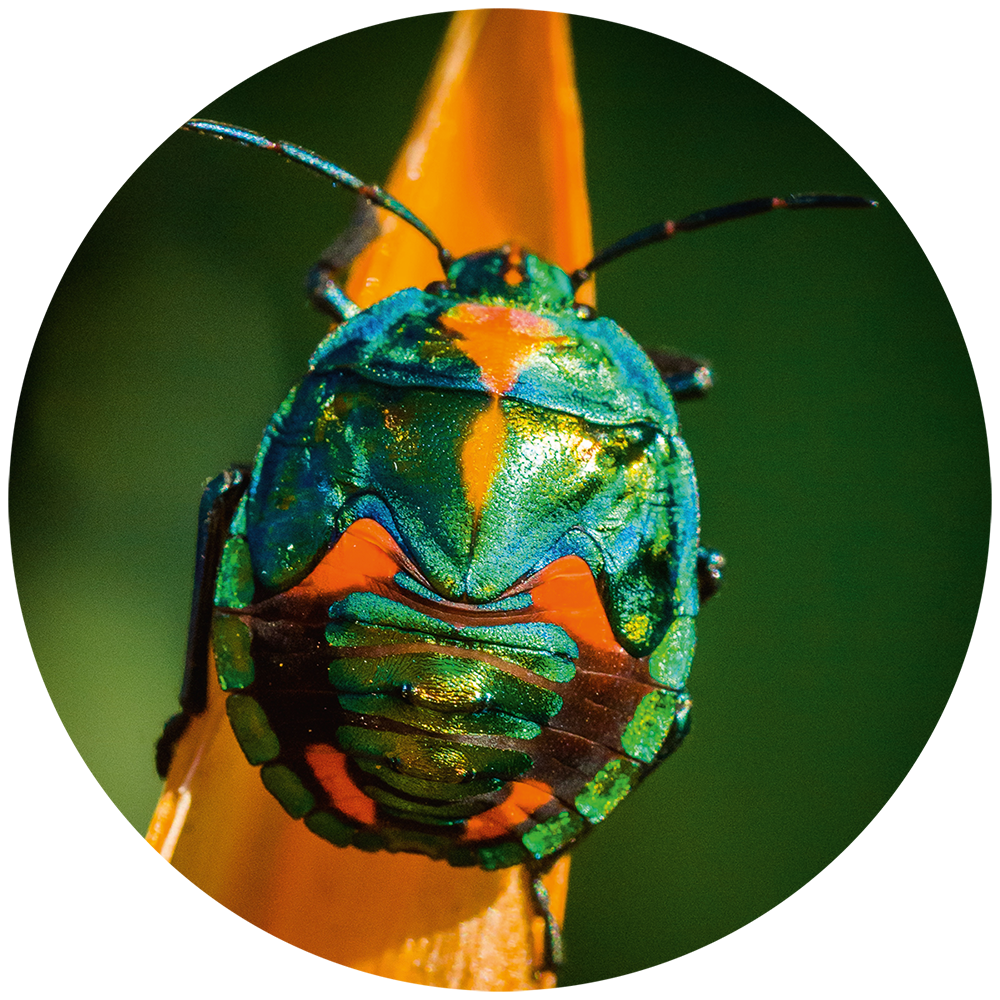
Isolating by-products – a major challenge
In the world of agriculture, there are increasing pressures to maintain or increase crop yields in the face of growing threats – whether from pests, diseases, competitive weed species or the changing climate. To minimize the effect of these threats, farmers need to deploy a range of methods to promote strong and healthy crop growth. Crop protection products such as herbicides, fungicides, insecticides and seed treatments are an essential part of this effort, and Syngenta works with farmers, researchers and agriculture experts to understand the challenges faced and to develop new or improved treatments.
As a heavily-regulated industry, crop protection products must meet numerous criteria before they can be registered for use, which includes rigorous tests to assess their safety for workers, the environment, crops and consumers. Some of these tests must be carried out on all components of technical-grade material of an active ingredient at, or close to, the 0.1 % weight level. However, obtaining these “by-products” in sufficient quantity and purity, is a big challenge.
Developing analytical solutions at Syngenta
Isolating these by-products in usable quantities is where separation scientists such as Louise Bacon come in. Louise works at Syngenta as the Team Lead for the Preparative and Isolation Chemistry Team, which sits within the company’s Analytical Solutions Group at Jealott’s Hill International Research Centre in Bracknell, UK. Her team assists their colleagues around the world with the toughest of separation challenges with the help of preparative-scale liquid chromatography.
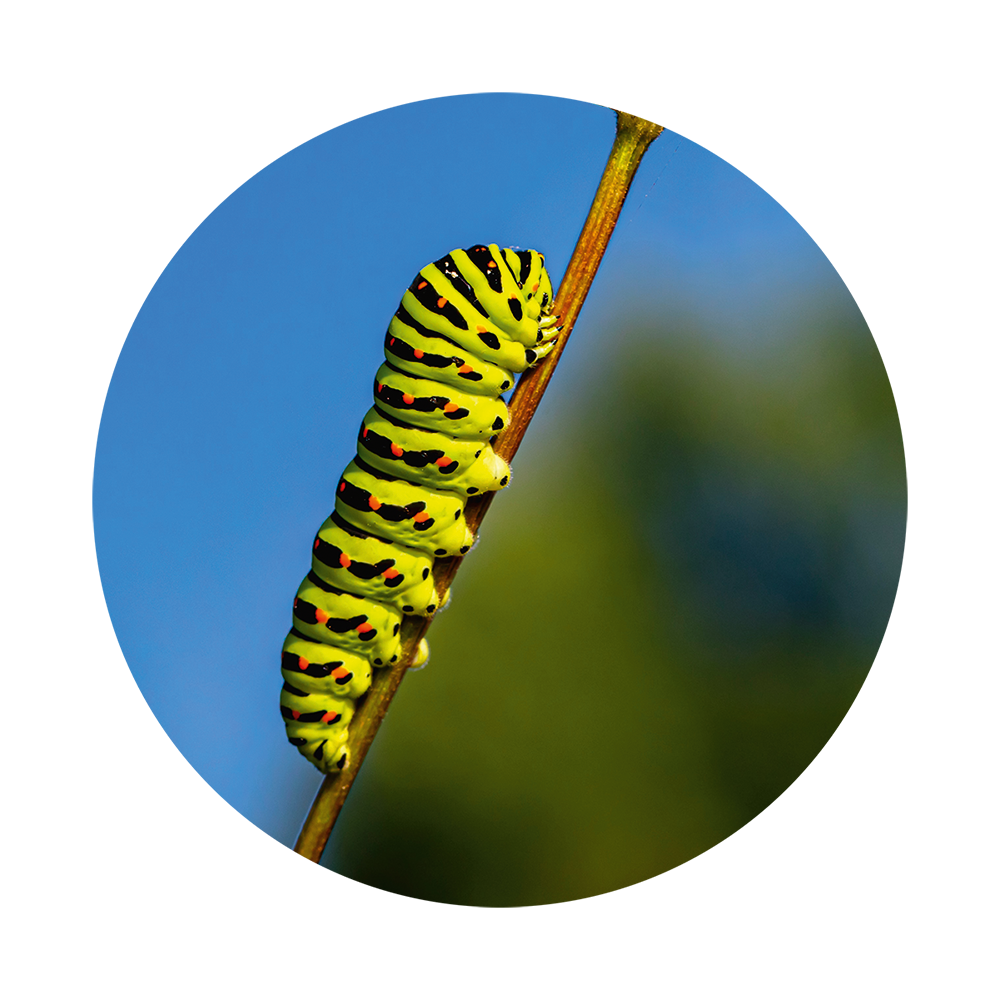
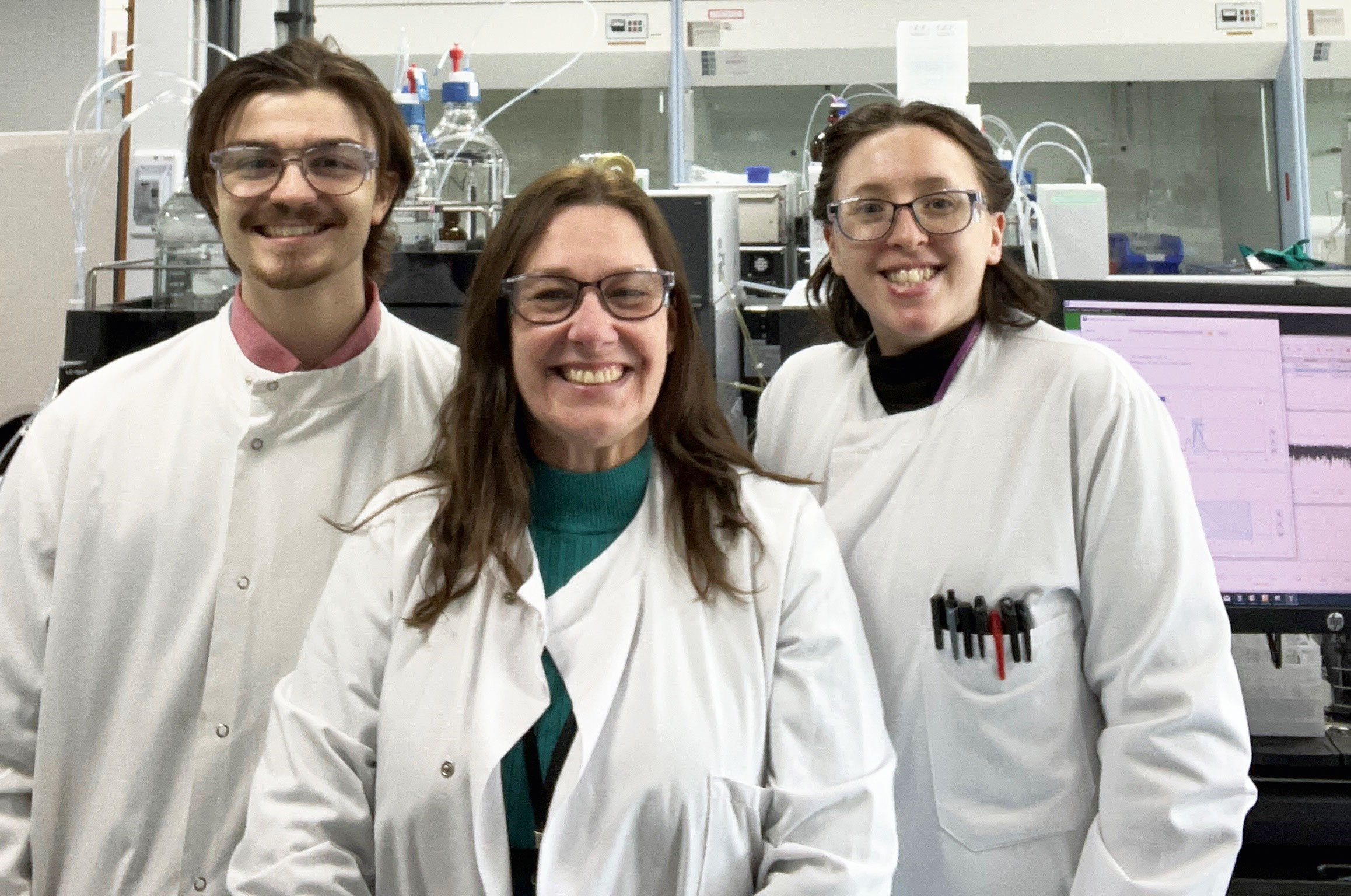
Louise has had several roles at Syngenta over the last 30 years and has been working full-time on the preparative side since 2016. She describes the sorts of projects that her team receives: “Most of our projects come from our ‘global analytical champions’, who are responsible for an active ingredient and all the associated method validation and regulatory work. As part of that, they may need our help to extract and purify milligram levels of an unknown by-product for identification. But more often they will need larger quantities of a by-product for use as analytical standards, extending up to the gram levels required for toxicity testing. For example, it’s not uncommon to have a by-product present at 0.5 % by weight in a product, and that requires a toxicity test on the pure chemical in order for the active ingredient as a whole to be registered”.
It’s this need for larger quantities, she explains, that presents the biggest challenge. “We’ll liaise closely with our chemistry colleagues to work out the best route to these by-products. The preferred route is synthesis because it’s quicker – but not everything can be synthesized, and even if it can, it usually results in an impure mixture. So we’re often asked to extract the pure by-product from these mixtures or from extracts or washes obtained from the original synthesis of the active ingredient”.
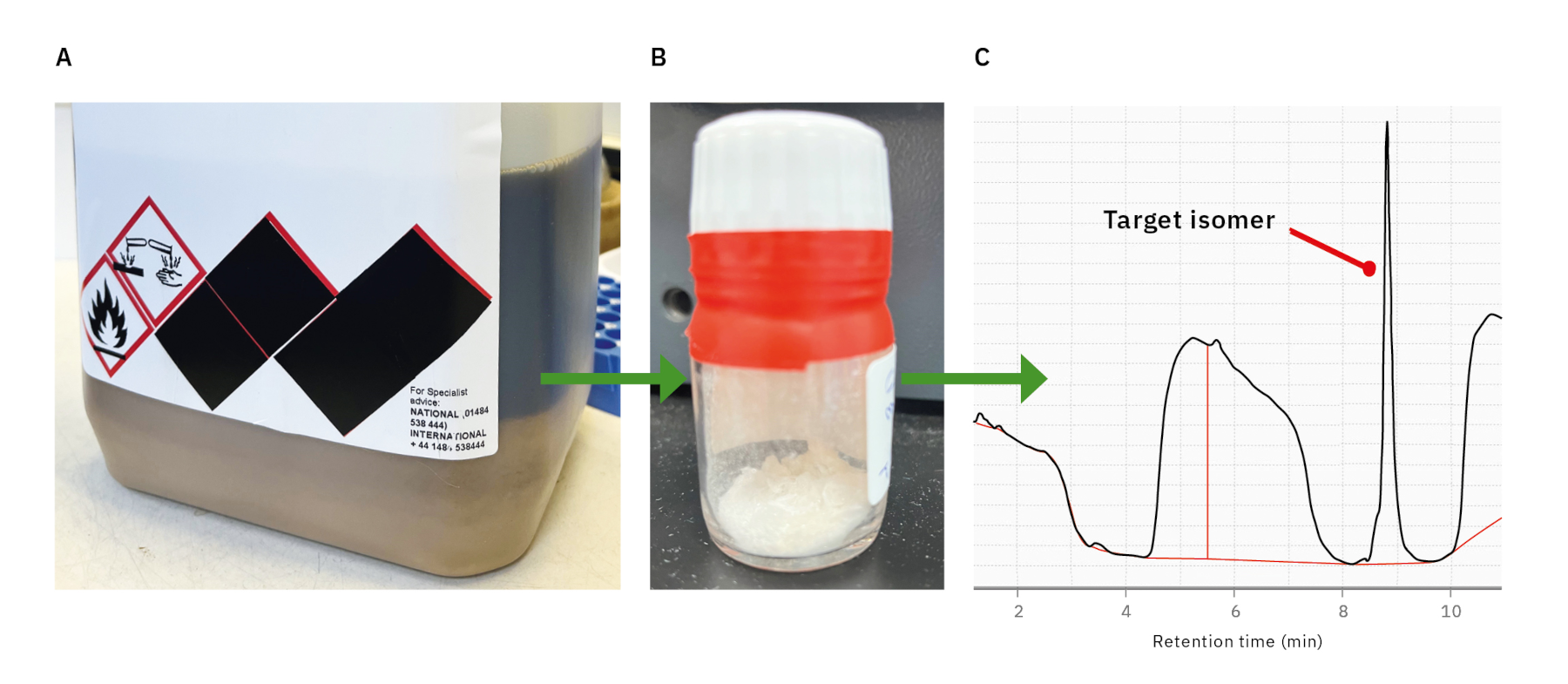
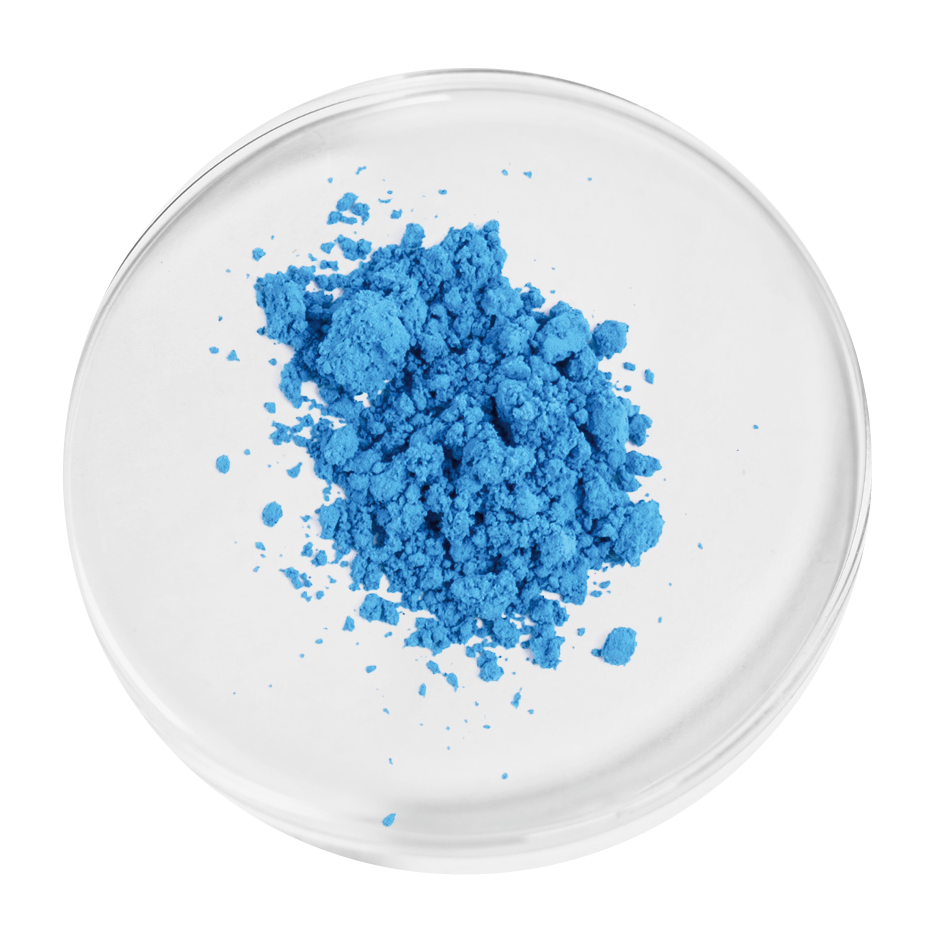
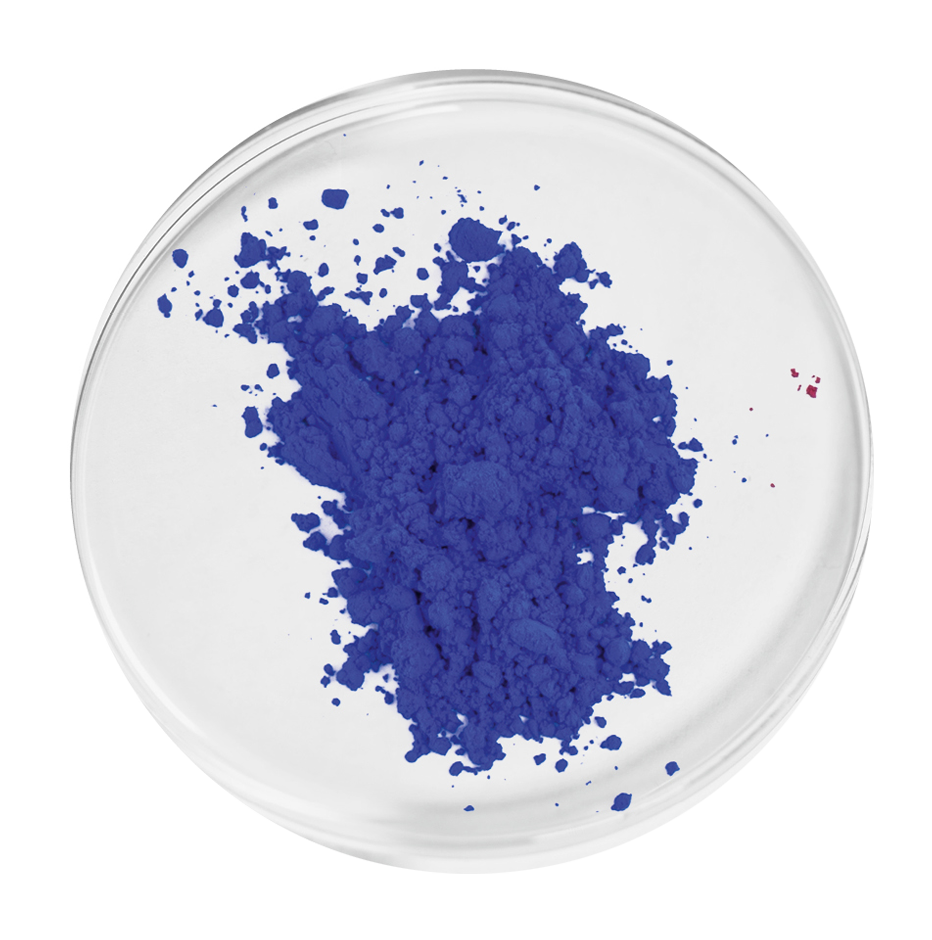

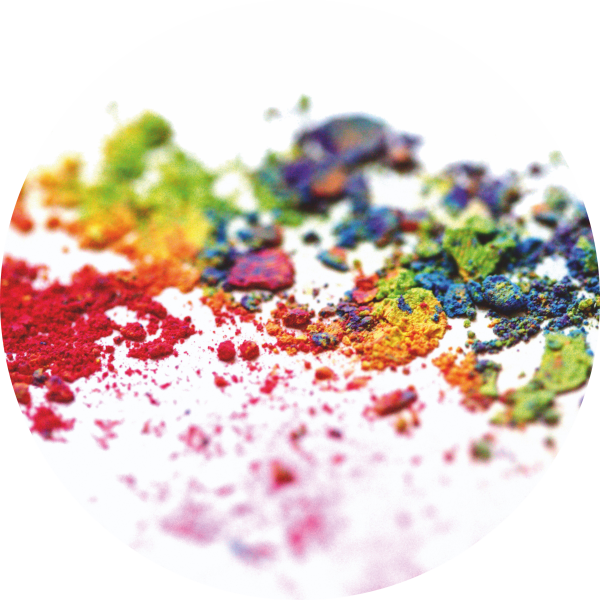
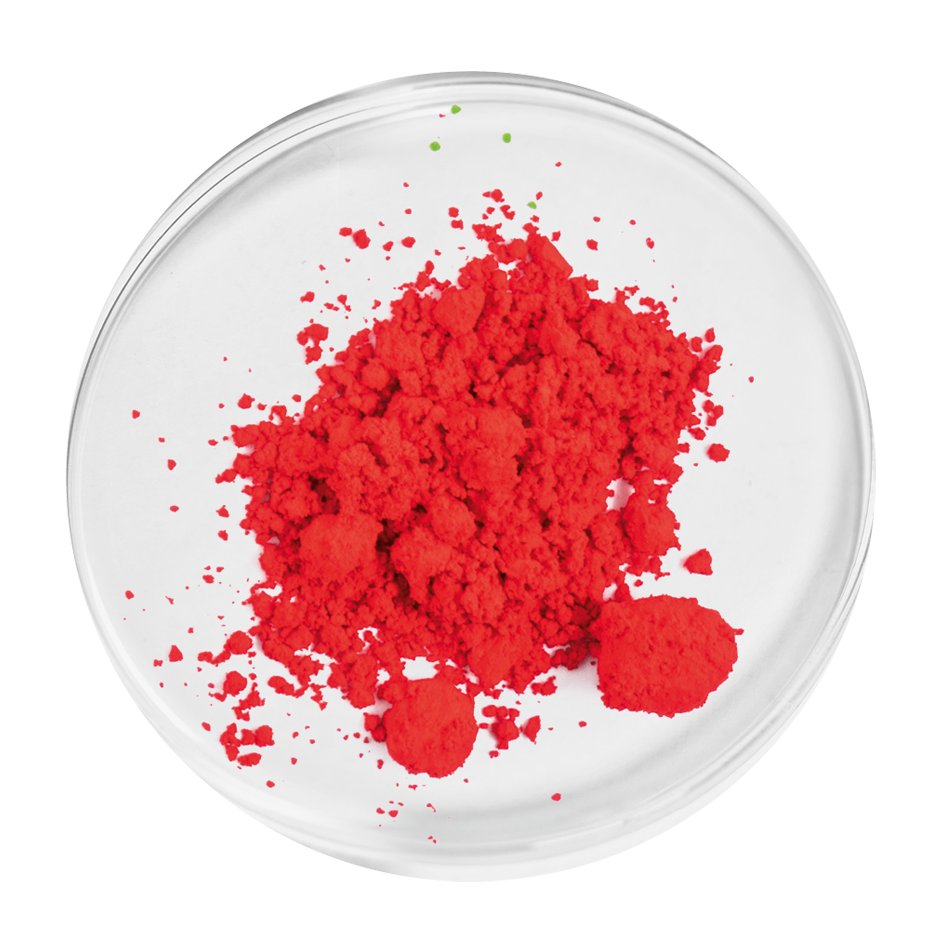
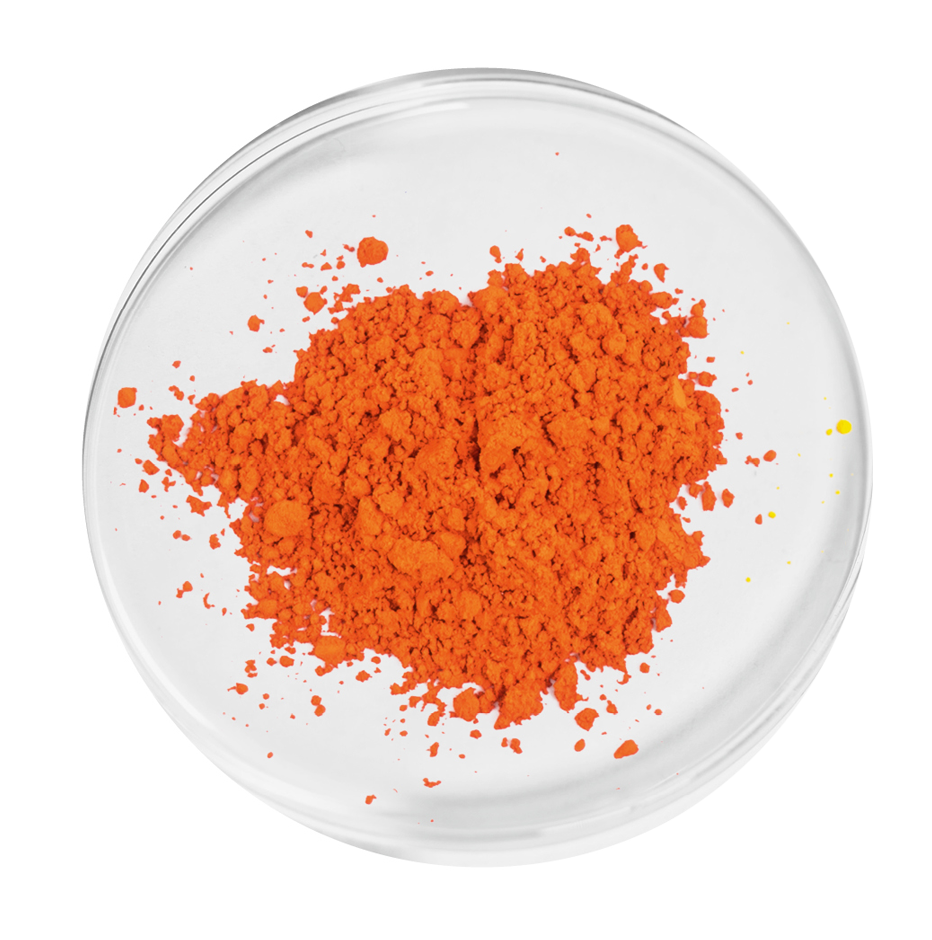
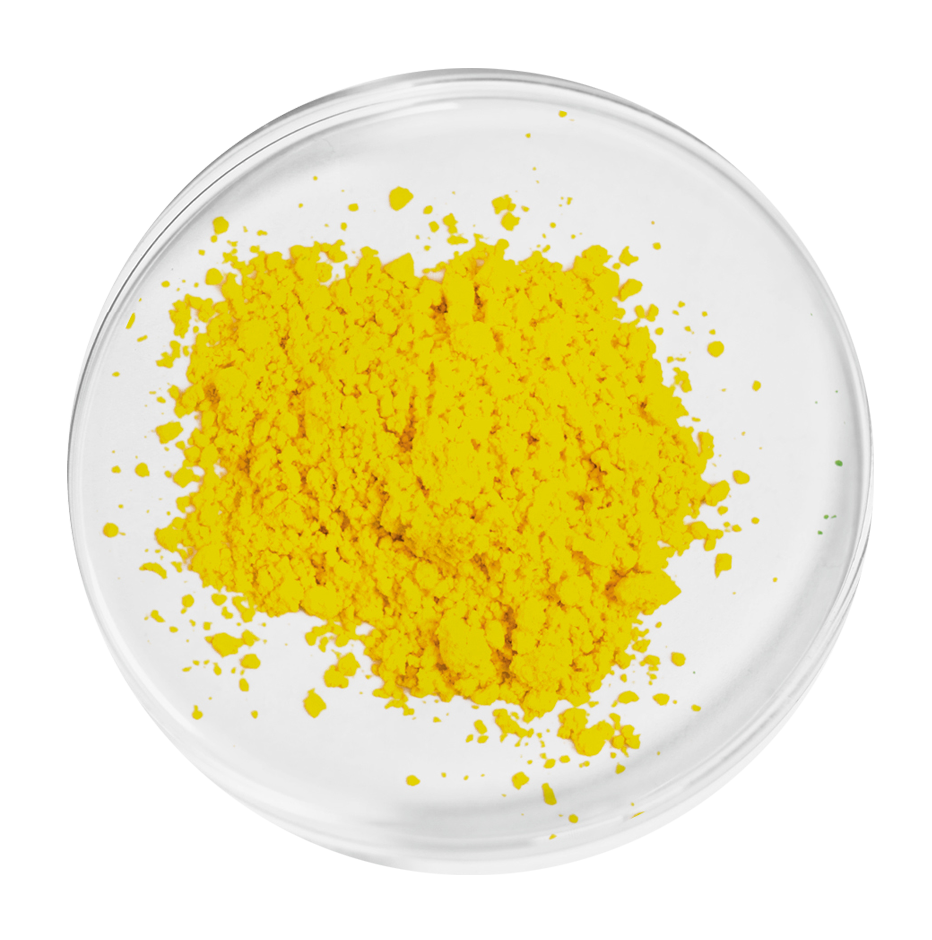
The value of ultra-fast preparative LC
Louise and her team usually like to tackle these purifications through a two-stage approach: “We’ve found it works best if we do a ‘rough and ready’ large-scale purification of the supplied material, for example to enrich it from 0.1 % up to 5 %, perhaps up to 20 % if we’re lucky. We then follow this with a ‘polishing’ step to bring it up to the required purity, which is usually 90 % or higher”.
This first step is the most challenging, Louise explains, because it involves dealing with such large volumes of material. “To take one example, we were working with an insecticide by-product that was a highly volatile acid, supplied at 0.3–0.4 % in acetic acid solution that also contained aliphatic components and salts. The request was for 800 mg, which we knew at the outset was going to be tough”, she says.
Their initial approach was to run the washings through an HPLC and collect/combine all the fractions. This was far from ideal, requiring 1,000 injections with a 22-minute run time, giving liters of extracts to deal with. Not only that, but subsequent processing was also difficult. Lyophilization didn’t work because the target compound was too volatile, while the alternative – extraction of the acetonitrile/water fractions from HPLC with dichloromethane (DCM) – gave mixtures that were difficult to evaporate down without losing material. Louise explains the upshot: “All this consumed 5 months of the team’s time and, to add insult to injury, the final material was only 55 % pure!”.
So when the request for a further 4 grams of the target compound came in, Louise knew they needed another, more automated approach: “The HPLC route was scarcely feasible at the smaller scale, and so obtaining more material the same way was clearly going to be impossible. But fortunately at about this time, in the middle of 2021, an opportunity came up to acquire a Shimadzu UFPLC instrument. We immediately saw how it could help us and jumped at the opportunity!”.
Shimadzu’s Ultra-Fast Preparative LC (UFPLC) works by automatically heart-cutting the fraction containing the target compound and trapping it on a short column, rather than leaving it to elute. Louise’s team realized that this would enable them to backflush off their target compound in acetonitrile, dispensing with the need for DCM extraction and leaving them with a solution from which the acetonitrile could be gently removed without problems.
Following some work to optimize the column to avoid co-elution of the analyte with a “hump” of unwanted material, the team finally found success, says Louise: “From 5 liters of washings, we obtained well over a gram of material, and the purity of the product was better than we’d achieved before. But more than that, we’d avoided all the manual handling, eliminated the problems with drying-down and reduced the processing time to a matter of weeks”.
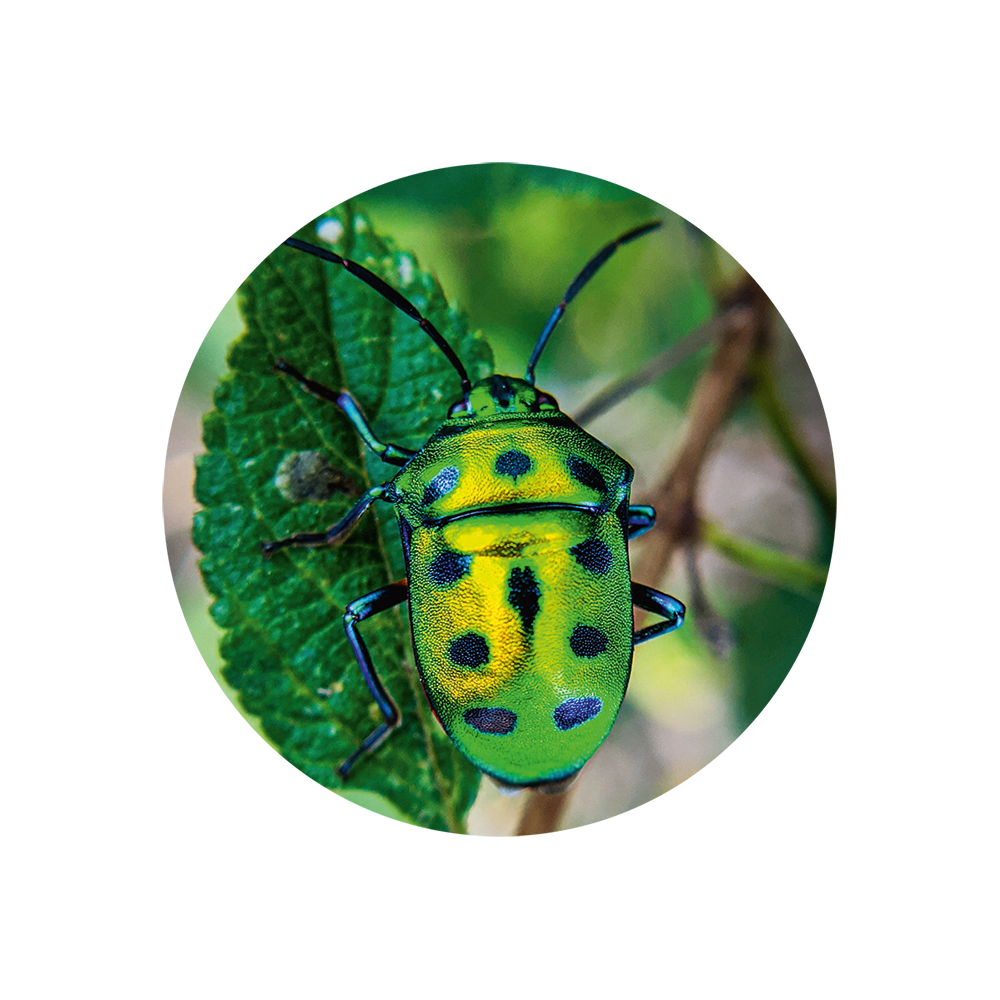
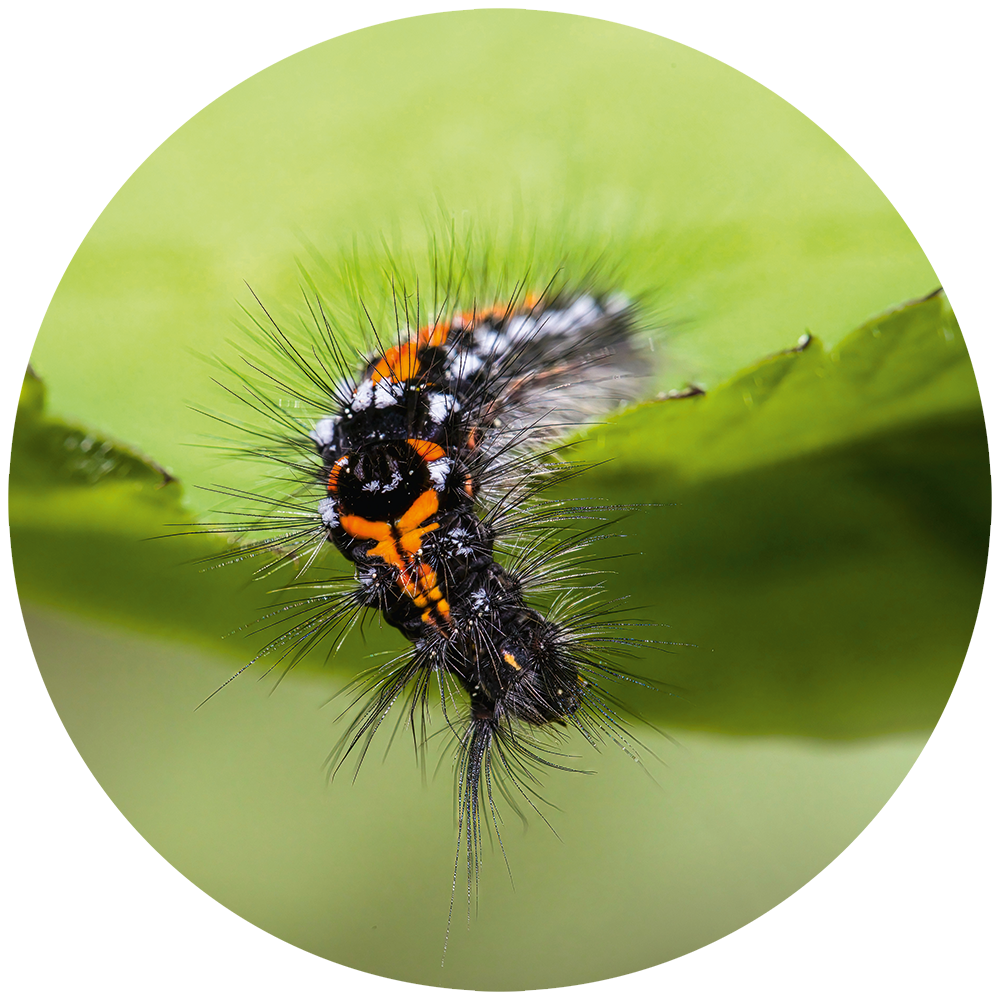
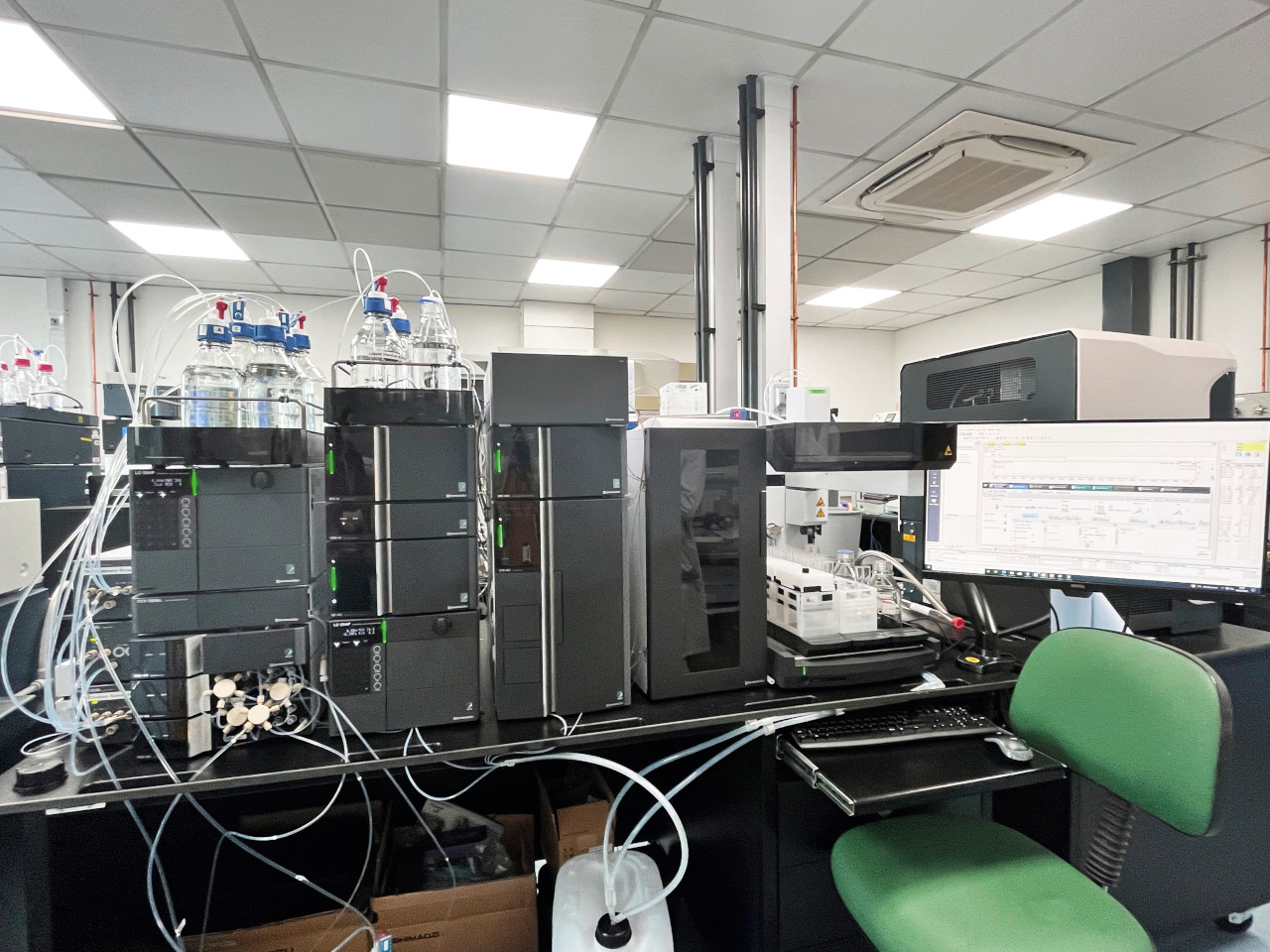
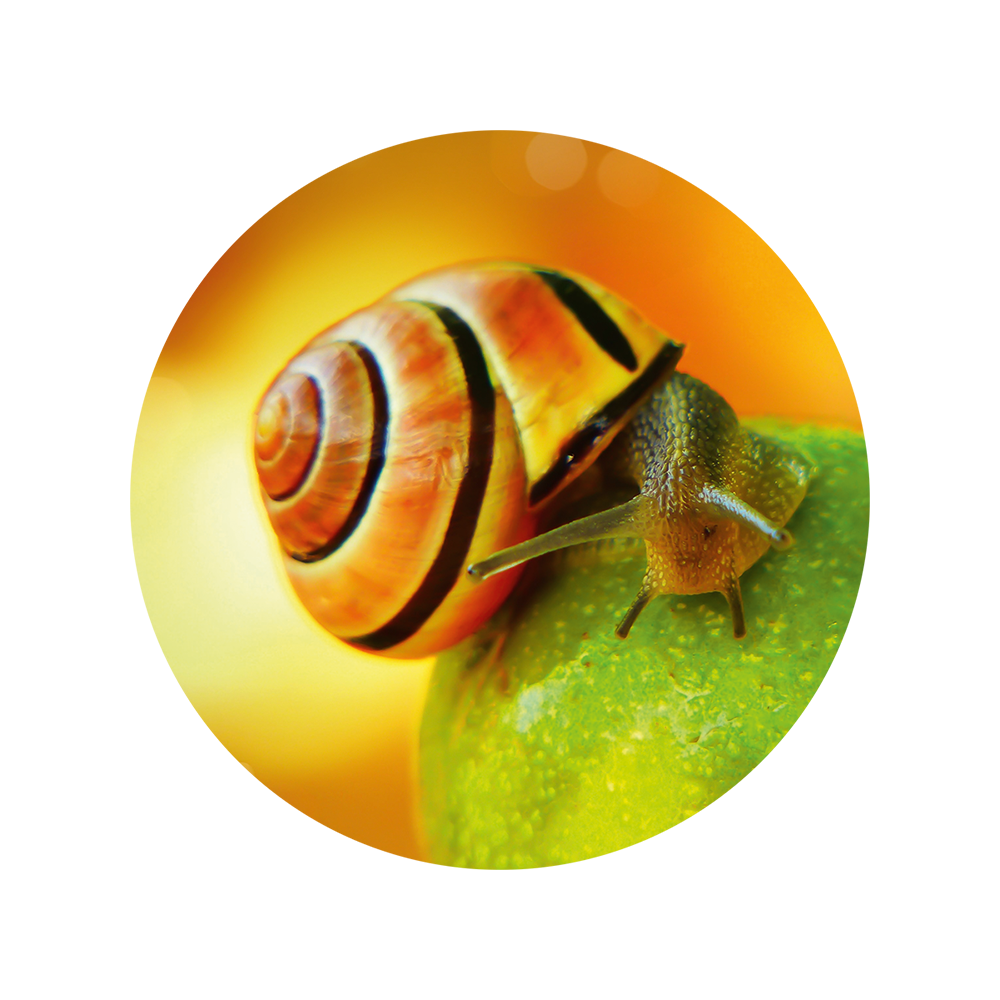
Automated fraction collection for faster turnaround
In fact, the efficiency savings with the first system were so good that Louise used it as an example to request the purchase of a second system – which was set up by the beginning of this year. So what will the team be using their new equipment for?
Louise says: “We see the greatest value of UFPLC in cases where we have large volumes of impure material requiring hundreds or even thousands of injections. Using HPLC would generate multi-liter quantities of fractions, which would slow us down because of the backlog of samples awaiting evaporation, especially when we’re being asked to collect multiple products. But with the Shimadzu system we can automate the collection of up to five fractions with no manual intervention”.
This, she says, makes it ideal for the initial clean-up and enrichment stage of a complex mixture. “We don’t even have to do a full separation – in a recent project on a herbicide by-product, we used a 50-mm column with a 5-minute run time, simply to remove the majority of the unwanted material and provide a small volume of a greatly enriched extract, which we could then ‘polish’ on one of our other preparative systems”.
She adds that the chromatographic reproducibility of UFPLC is critical to the ability to automate the collection of fractions – because the team are looking at products that are scarcely off the baseline, they have to rely on known retention times rather than gradient information. Another benefit is the small fraction volumes: “In the herbicide project, the target material wasn’t particularly stable. It was therefore really useful that we were able to get it into small volumes so that subsequent processing steps were as quick as possible”.
Reducing solvent usage
An important consequence of the team’s new equipment is not only product quality and turnaround time but reducing the environmental impact of their methods. This is a result of being able to use short columns and short run times, with a consequent reduction in the amount of solvent they’re using.
“Reducing our solvent usage is a major benefit of using UFPLC, and one we’re going to be looking at more”, says Louise. “On a prep HPLC method, you might be running thousands of injections on a 20-minute method at 50 mL per minute – which generates a vast amount of solvent to evaporate and ultimately dispose of. But with UFPLC, we reduce that need for solvents and the associated energy costs in evaporating them, as well as being able to use more environmentally benign solvents”.
In fact, this mission to reduce solvent usage is also a priority for Syngenta because it makes a significant contribution to the company’s sustainability goals. Supporting this, Louise’s team have a student on an industrial placement from Imperial College London, who will be using the new UFPLC systems to identify where the biggest solvent reductions can be made.
Making life easier
In conclusion, says Louise, with the help of the Shimadzu UFPLC, they’ve been able to achieve what was previously very difficult – the extraction of sub-percent levels of by-products from very complex mixtures, all while keeping solvent usage down, minimizing degradation of the target compounds and reducing manual processing to the bare minimum. As she concludes, “It’s been brilliant, absolutely brilliant, and saved us so much time!”.
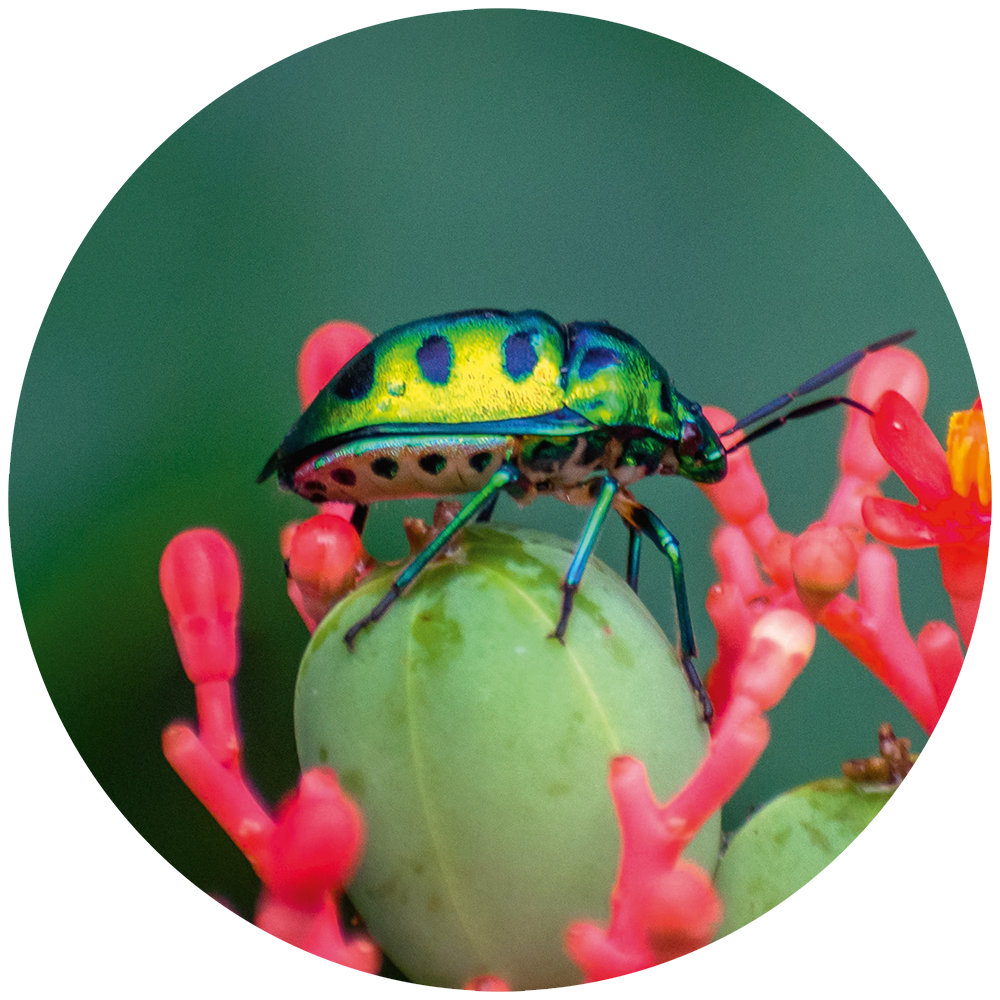