Low carbon, big impact: making the most of biowaste
Making useful materials from biological waste streams using pyrolysis
Dr. Daniel Nowakowski, Aston University, Energy and Bioproducts Research Institute
Pyrolysis of bio-derived waste has the potential to provide a lower-carbon, more sustainable way of producing chemicals that are currently made from petrochemicals. But with biowaste feedstocks being so diverse, how can we determine the best use of a particular resource? We talk to Dr. Daniel Nowakowski at Aston University’s Energy and Bioproducts Research Institute (EBRI) about the challenges faced when thermally processing biowaste – and how collaborating with Shimadzu is helping him and his team to maximize the potential benefits of diverse feedstocks.
The diverse composition of biowaste
The term “biowaste” covers a wide range of materials – from crop stalks to woodchip and from spent hops to seaweed. But what it all has in common is that it was recently living material that was sequestering carbon from the atmosphere and so inherently avoids the large CO2 footprint of fossil fuels.
Society has long used biowaste in the form of compost for improving or fertilizing soils, or for releasing heat by burning. But in the last 20 years, there has been growing realization that biowaste can also be used to generate useful chemicals by subjecting it to high temperatures in the absence of air (known as pyrolysis).
These products can be very varied, says Dr. Daniel Nowakowski, an expert in pyrolysis at Aston University, UK: “By heating up biowaste in a carefully controlled fashion, we can generate solids, liquids and gases with a wide range of interesting uses.”
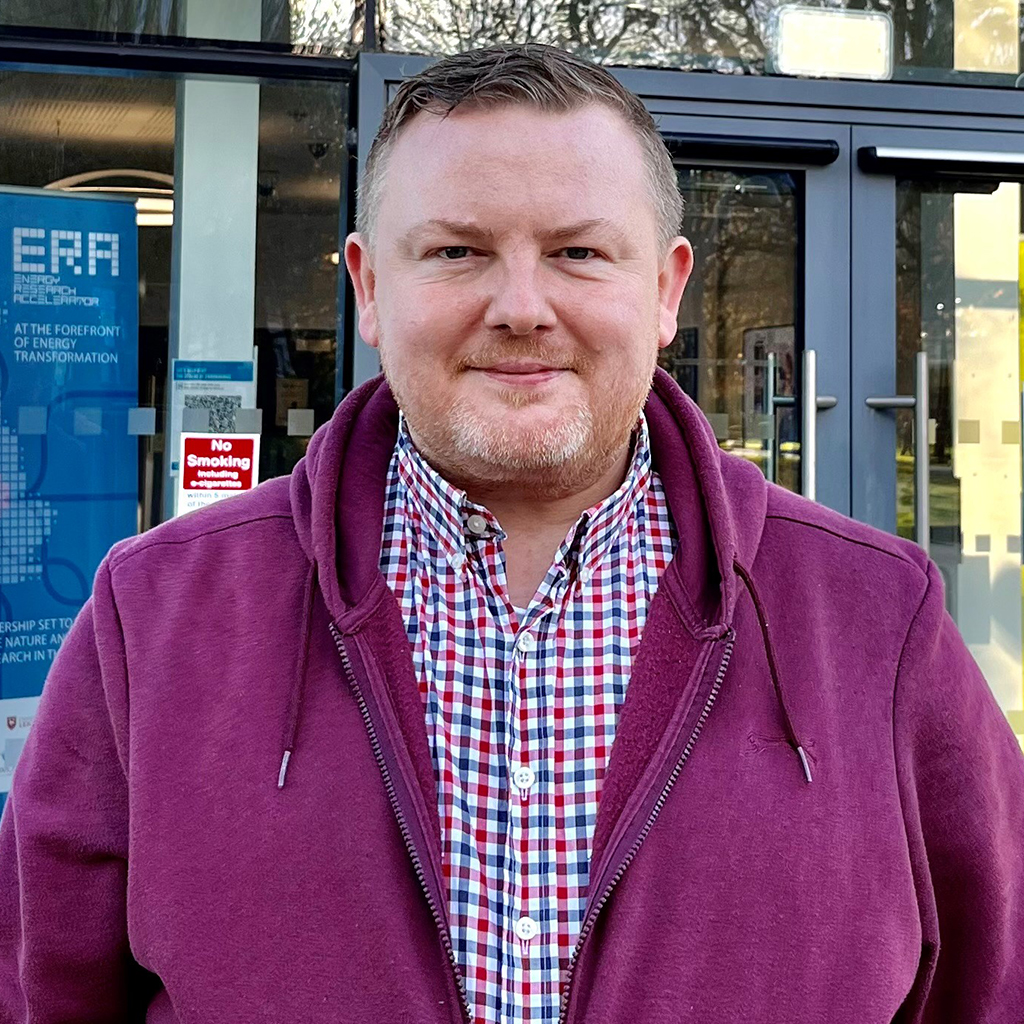
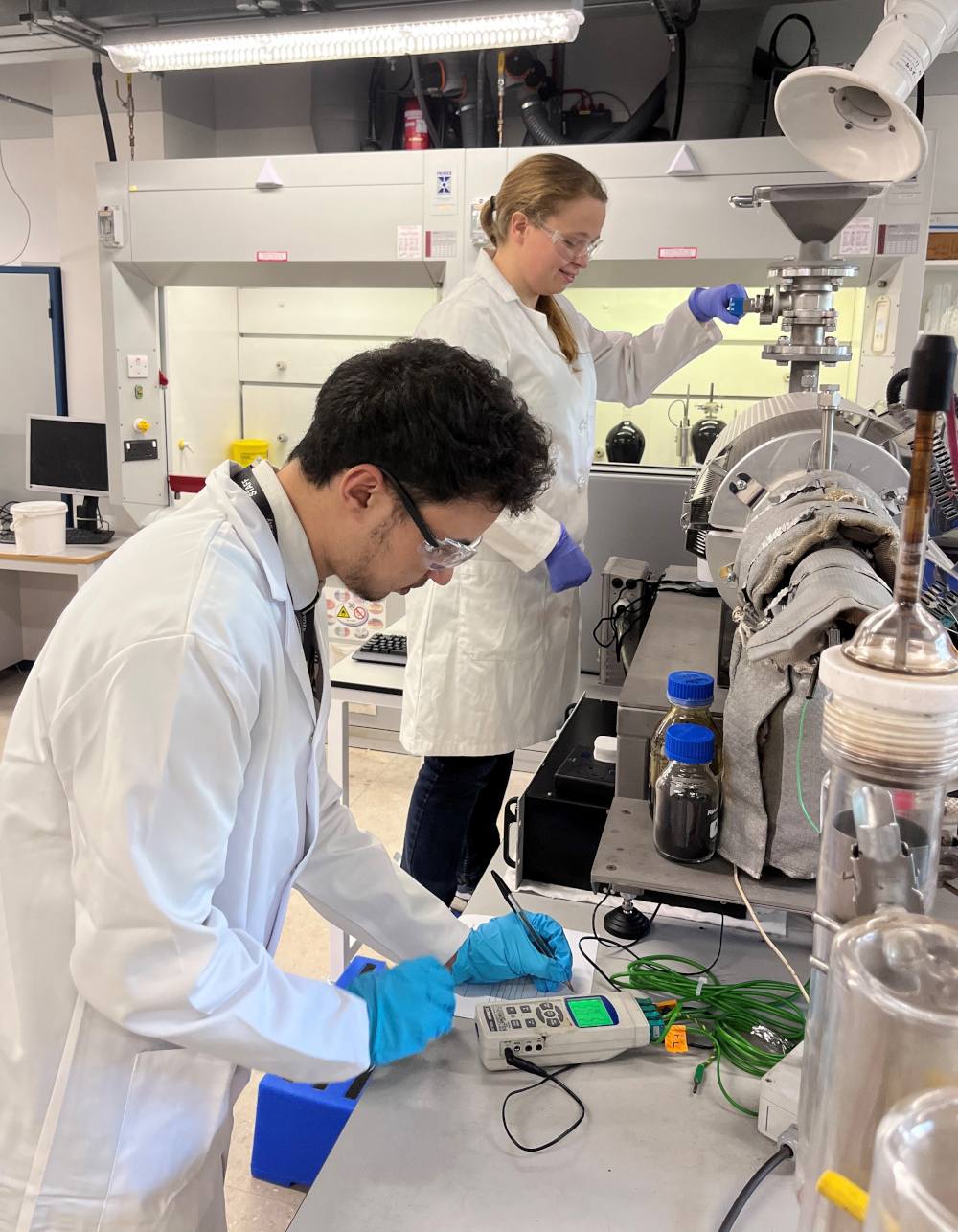
Investigating feedstock to derive the maximum benefit
As Lecturer in Chemical Engineering and Applied Chemistry at Aston’s Energy and Bioproducts Research Institute (EBRI), Dr. Nowakowski has first-hand knowledge about the types of biowaste sources and the ways in which the resulting products can be used – from carbon-storing soil conditioners to sustainable fuels.
This knowledge is put to use every day, not just through the team’s fundamental research but through their project work for government agencies, organizations and companies looking to do more with their biowaste. When they’re given a biowaste sample to investigate, he says, we ask one question: “How can we tailor the pyrolysis process to derive products with the greatest value or benefit?”
For example, he says, they might want to maximize yields of a particular product or eliminate an unwanted contaminant. “Working out the processing conditions that will do this requires experience and research but also a lot of experimentation: a single Ph.D. student can work for three years on optimizing the yield of a single component from a pyrolyzed feedstock!”
Pyrolysis – process and products
Before going further, it’s worth first understanding what pyrolysis is. Otherwise known as “heat treatment”, pyrolysis involves raising the temperature of a material in a reactor to 400–600 °C in the absence of oxygen. The material needs to be fairly dry, with typically less than 20 % water, to avoid compromising energy efficiency and causing phase separation of pyrolysis liquids.
“This closely mirrors the age-old process of making charcoal,” says Dr. Nowakowski, “but with much greater control over the conditions.” Also, he adds, nothing goes to waste: “Unlike in conventional charcoal production, we’re not just interested in the solid matter left behind – we also capture all the vapours and gases emitted in order to extract value from them too,” he explains.
During the pyrolysis process, there is extensive rearrangement and degradation of the bonds in the lignin, cellulose and hemicellulose and other compounds that make up a typical biowaste feedstock.
The pyrolysis process leads to the production of three classes of materials:
- Biochar is a highly porous form of carbon and typically takes the form of a black powder. It’s primarily of interest as a soil conditioner that can store carbon in the soil for extended periods, in a process known as carbon sequestration and storage (CCS). There are numerous standards for biochar, and biochar classes have also been recognized on the basis of the carbon content, particle size and presence of plant nutrients such as potassium and nitrogen. Biochar can also be “engineered” further into catalyst supports, polymer fillers and absorbents for heavy metals.
- Bioliquids contain a complex mix of carboxylic acids, phenols (and their derivatives), esters, ketones, anhydrides, ethers and oxygen-containing heterocycles. During pyrolysis, they’re released as vapours but are subsequently condensed into liquids. The water-miscible (aqueous) fractions, because of their acid content, are also known as “wood vinegar”, which has attracted interest as a fungicide and plant growth enhancer. The water-immiscible (“organic”) fractions are rich in aromatic compounds. These can either be separated from each other and used as chemical “building blocks” or catalytically upgraded to remove the oxygen atoms and give hydrocarbon fuels.
- Pyrolysis gas (also called “pyrogas”) includes methane, ethane and other hydrocarbons up to C5, hydrogen, carbon monoxide and traces of carbon dioxide. Gaseous hydrocarbons can be used to fuel the pyrolysis reactor, while hydrogen and carbon monoxide (syngas) can be used to produce ammonia or methanol. Hydrogen is also of interest as a “green” fuel for transport, particularly for heavy goods vehicles (for which electrification is not currently practical).
Tailoring the pyrolysis process
The amounts of biochar, bioliquids and biogases produced vary greatly depending upon the volatile content of the original material and the processing conditions, says Dr. Sarah Asplin, a Research Associate at EBRI, who is using her knowledge and skills from her Ph.D. in the field of biomass pyrolysis. She explains that slow, relatively low-temperature pyrolysis of biomass in a batch reactor might yield up to 50 % biochar and 25 % each of bioliquid and biogas. In contrast, quick, high-temperature pyrolysis of high-quality woodchip in a fluidized-bed reactor could result in up to 75 % bioliquid, with most of the remainder being gases and very little biochar.
Along with feedstock quality, all these factors feed into decisions about what to do with a particular feedstock, says Dr. Asplin: “For example, clean feedstocks, especially those that are lignin-rich, are generally best turned into biochar because of the low loadings of contaminants in the final products, whereas low-quality feedstocks are better suited to bioliquid or biogas, because clean-up by liquid-liquid separation, distillation or downstream processing is a necessary part of producing them.”
A relatively new development in processing technology is so-called “intermediate pyrolysis”, whereby the feedstock is placed on a moving bed, she adds. “This allows a high degree of control over the process temperatures and times, making it possible to fine-tune the conditions to optimize the desired products.”
Quick initial analysis – combining the right methods
To properly understand the potential of biomass and other organic waste requires an in-depth study of their chemical composition, says Dr. Nowakowski: “You can’t simply get away with applying a single analytical method!” In fact, his understanding of this aspect extends beyond his research, because he also has overall responsibility for the wide range of analytical equipment at EBRI.
One of the first steps when understanding the potential of a new material, he explains, is to carry out a thermal degradation study. This involves heating a small portion (about 10 mg) up to about 750 °C in a thermogravimetric analyzer and monitoring how the mass changes as the temperature rises, giving the researchers an initial idea of its volatile content and solid residue. At the same time, the gases released can also be sent straight to a detector using a technique known as evolved gas analysis, again to provide a first impression of what the sample contains.
More information on the products obtained from thermal degradation happens through micropyrolysis-GC-MS. This uses what is in essence a miniature version of the full-scale pyrolysis equipment, with a GCMS fitted to the outlet, configured to analyze the vapour-phase products. The research team at EBRI have two such “pyroprobe” systems, with the one they use the most being a multi-shot micropyrolyzer from Frontier Laboratories partnered with a GC-MS.
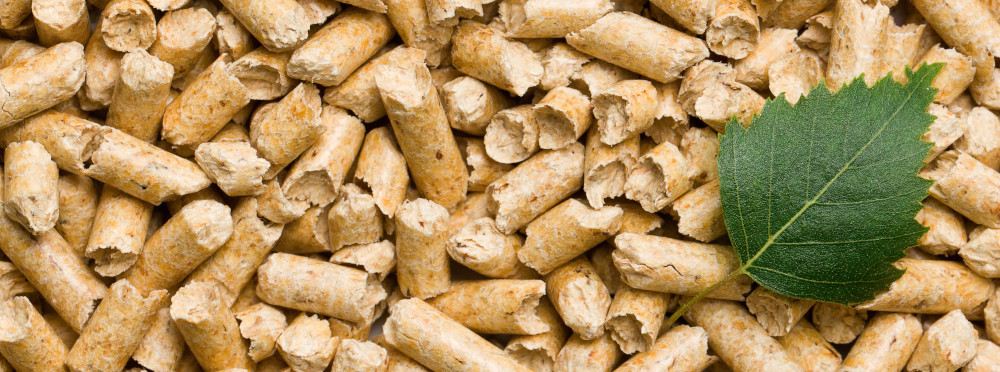
The advantage of this setup, says Dr. Nowakowski, is its speed. “In just an hour, you can complete the preparation and analysis of a test sample and get an idea of the vapours that could be obtained from the feedstock,” he explains. By adding an internal standard, the amounts of given products can be quantified and a preliminary assessment of product yields obtained, he adds.
The next steps depend on the outcome of those initial investigations, says Dr. Nowakowski, but they will often employ elemental analysis or TOC analysis to find the “total organic carbon” present in the sample. Another method useful at this point is calorimetry to find the heating value. “Both these techniques can be useful in discussions with clients who might be wondering whether it’s worth simply burning the biowaste to release its energy content,” he points out.
Detailed analysis of the product mix
When it comes to a more detailed analysis, the team turn to a range of chromatographic techniques to cover every possible combination of feedstock type, mixture complexity and analyte chemistry.
- GC-MS/FID: By splitting the column outflow and sending it two ways, combines the compound-identifying capabilities of MS with the quantitative performance of FID. There are two such systems at EBRI – one with a one-liquid autosampler for investigating bioliquids and the other with a headspace-configured “pyroprobe”.
- GC-FID (gas chromatography-flame ionisation detection) offers a simpler and more accurate quantitation than GC-MS and is used for quick analysis at every stage of biowaste processing. At EBRI, there are a total of six systems that are ready to go with different chromatographic columns, plus two systems that also have the capability for TCD (thermal conductivity detection). This is used instead of FID when the analytes don’t contain a carbon-hydrogen bond, making it suitable for analyzing permanent gases such as hydrogen, carbon monoxide, carbon dioxide, oxygen and nitrogen. One of these GC-FID/TCD systems has a high-temperature injection port for analyzing the heaviest hydrocarbons.
- GC-BID is another system at EBRI that’s tailored to gas analysis and uses a BID (barrier ionization detector), which offers much lower detection limits than TCD for permanent gases.
- HPLC (high-performance liquid chromatography) is the standard method for separating gram-quantities of complex liquid mixtures, and there is a system at EBRI used for analyzing aqueous phases from the pyrolysis process, especially organic acids.
As is clear from the above list, Shimadzu systems are a big feature of the labs at EBRI, with over 12 instruments in total. “Having the equipment from the same manufacturer means that we can use the same software and the same analytical processes – which is good both for productivity and training,” says Dr. Nowakowski.
And, as Dr. Nowakowski states, this equipment and expertise is shared with academic institutions, R&D centers and industrial partners at home and abroad – such as the Biochar CleanTech Accelerator. “Doing this allows us to exchange scientific knowledge, build teams for larger-scale research proposals and most importantly focus on applied research,” he explains. “By carrying out such ‘proof-of-concept’ studies, we can make big strides towards product certification and commercialization.”
EBRI’s impressive array of analytical equipment supports is also available to young researchers, he adds. “We have links with many academic institutions from the UK and Europe – all of whom can apply to use our equipment,” he says. “So, at any one time, we might be hosting several Masters and Ph.D. students, based here for anything from a few weeks to several months, and getting the benefit from our instrumentation.”
Biochar as a soil improver and polymer additive
So what projects is Dr. Nowakowski currently involved with?
One project with clear benefits on the ground, he says, is a collaboration with Birmingham City Council. This involves generating a biochar-based soil improver from the large amount of tree and shrub cuttings that the council produces from the parks and gardens that it maintains. Called the “Urban Biochar and Sustainable Materials Demonstrator” project, the cuttings are taken to the council-run Cofton Nursery in Longbridge (Birmingham, UK) and first screened to remove leaves and other compostable material. The larger, more woody material is shredded and pyrolyzed on-site in a unit installed in a shipping container, yielding biochar. This is used in various projects locally to improve soil structure and boost plant growth while also incorporating the carbon in a form that is not readily biodegraded and so providing a role as a “carbon sink”.
Dr. Nowakowski explains that EBRI was closely involved in optimizing this setup: “At the outset of the project in 2019, we investigated the potential for using biochar in a wide range of applications. We did quite a bit of large-scale work to find the optimum process parameters to produce larger quantities of biochar,” he says.
Another use of biochar that Dr. Nowakowski’s team is investigating relates to its use as a filler in plastic composites used (for example) in 3D printing. This is relevant because, as he explains, biochar isn’t always 100 % carbon: “Depending on the feedstock and process conditions, cold spots can arise in the biochar, which can trap small amounts of low-volatility compounds such as polycyclic aromatic hydrocarbons, which are toxic. These would normally remain bound to the biochar but if you’re using it as a filler in plastic, which then ends up being heated during processing, it could release these chemicals and cause a safety issue.”
To study this effect, he adds, the researchers use the “pyroprobe” setup to assess the thermal stability of small samples of biochar-modified plastic pellets to be sure that the product is going to be safe for the purpose.
A typical example showing the results of analyzing a sample of biochar by GC-MS to assess its purity. In this case, the compounds highlighted would be undesirable in the final product because of their known toxicity; work carried out at EBRI aims to understand the pyrolysis conditions that lead to these contaminants and minimize them. The analysis used a Frontier Lab EGA/PY-3030 double-shot analytical pyrolyzer, close-coupled with a GCMS-QP2010 SE system.
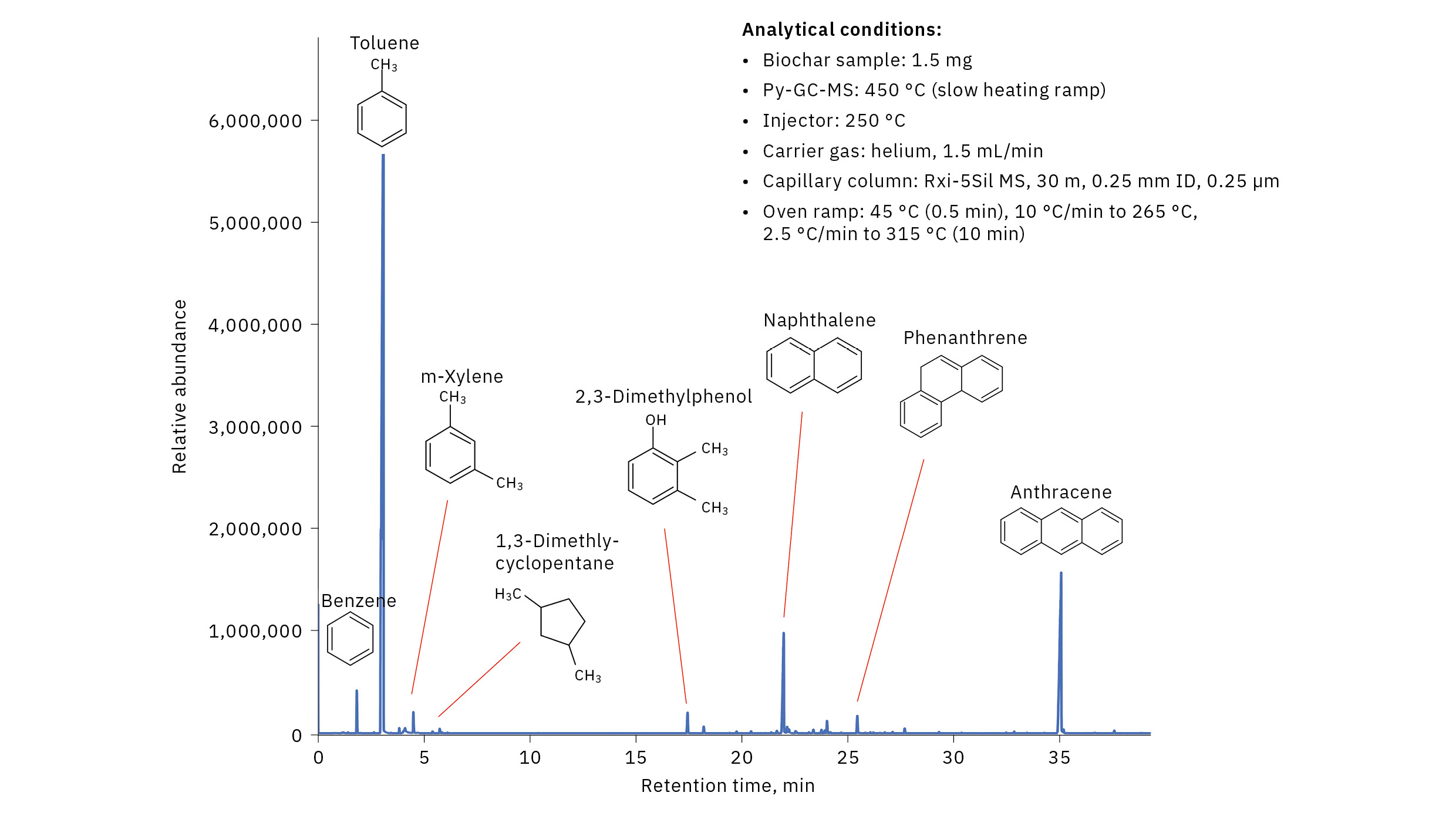
Bioliquids as fuel additives and antifungal agents
Bioliquids are also a fruitful area of study, says Dr. Chris Thomas, Knowledge Exchange Associate at EBRI and another former Ph.D. student of Dr. Nowakowski. “A particular interest at the moment is what we call the ‘catalytic upgrading’ of pyrolysis liquids. This involves taking the crude, water-immiscible pyrolysis oil and treating it with hydrogen under high pressure and temperature with a catalyst. That removes oxygen from the oxygen-containing compounds, giving us an upgraded pyrolysis liquid, which can then be distilled and combined with conventional biorefinery streams for production of biofuels.“
For this application, explains Dr. Thomas, the boiling-point distribution is of particular interest, but distillation doesn’t work well on small scales, and optimizing the pyrolysis-upgrading process on a large scale would be expensive and time-consuming. So, to predict the boiling-point properties quickly from smaller-scale experiments, he used one of the GC-FID systems at EBRI to obtain a chromatogram of the crude liquid and then applied the SimDist software tool to interpret the results.
Dr. Thomas is keen to emphasize the benefits of this approach: “Directly from what are often very complex chromatograms, we can use this ‘simulated distillation’ method to help us understand at what temperature the different components in a mixture will boil off at. The resulting distillation curve shows us the proportion of each component that evaporates at different temperatures, which is crucial for checking the quality of biofuels and other bioliquid-derived chemicals.”
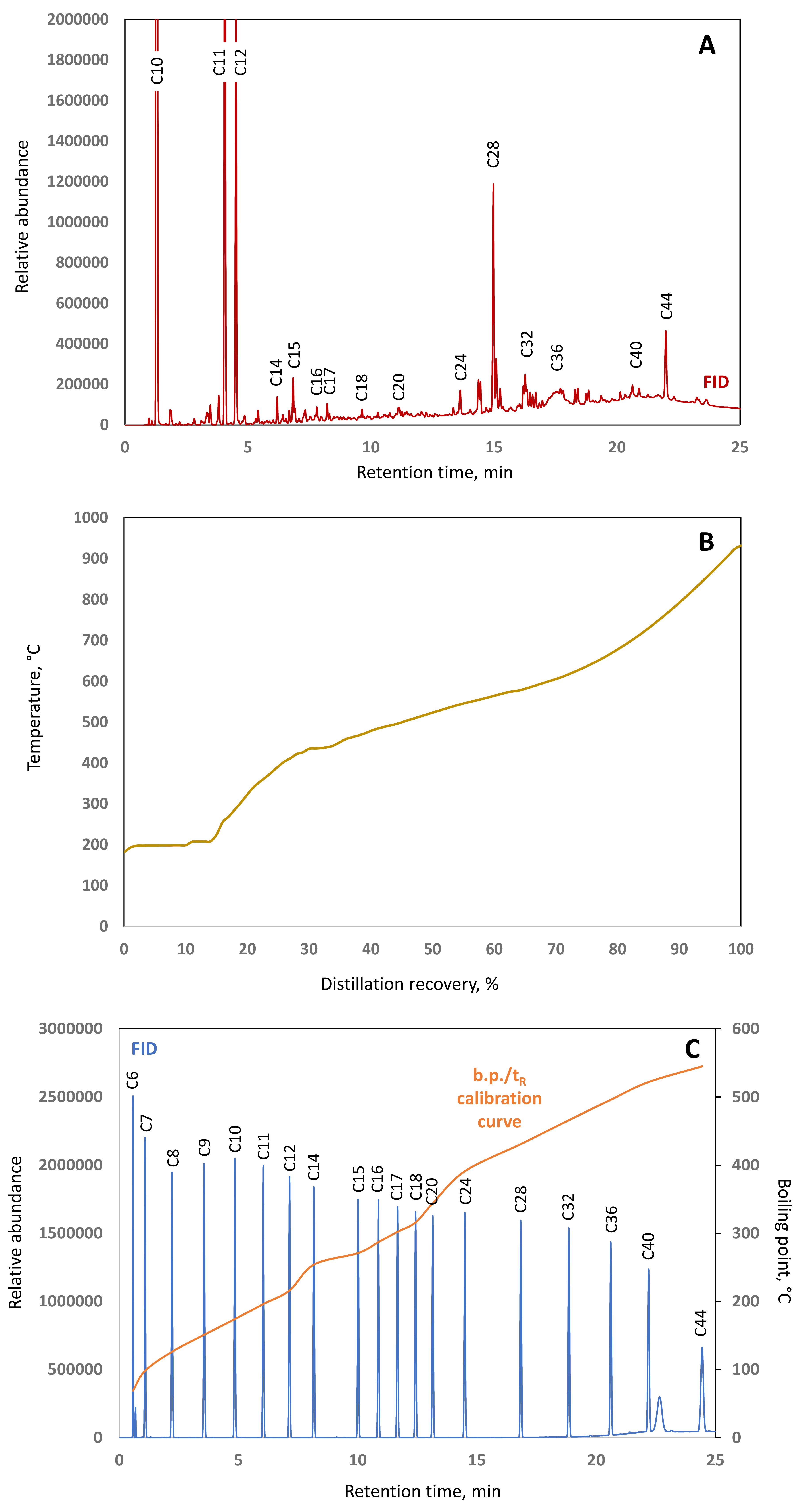
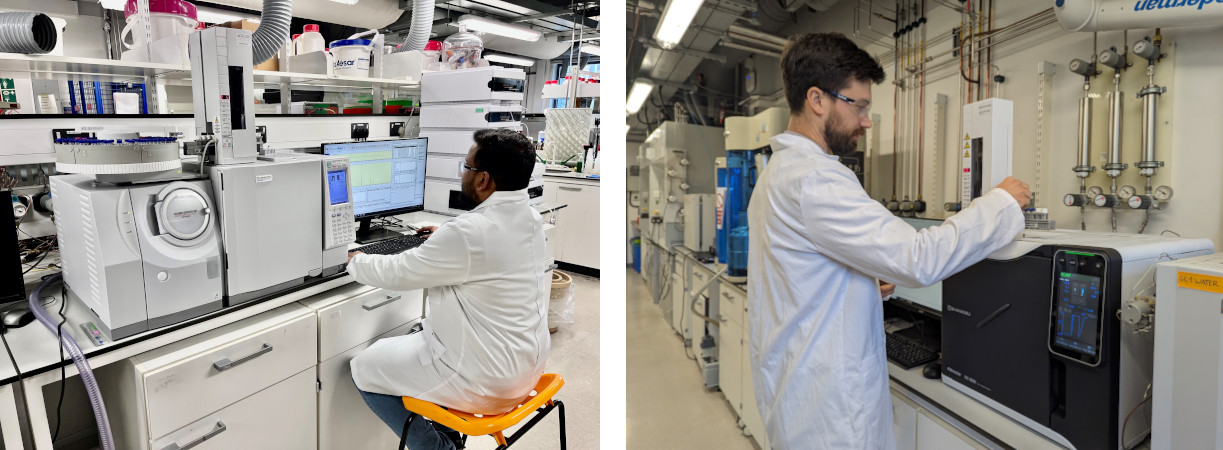
Another application of bioliquids that Dr. Nowakowski and colleagues are working on is so-called “wood vinegar”. This is a light-colored aqueous liquid dominated by carboxylic acids, including acetic acid, formic acid and propionic acid as well as some phenolics and many other organic compounds about which little is known.
Dr. Nowakowski explains: “These liquids have received a lot of hype as ‘natural’ antifungals and antibacterials, but there’s little information about exactly what they contain, let alone studies into their environmental and health impacts. So, a focus for us at EBRI over the coming year or so will be using our HPLC and GC-MS instruments to understand these liquids in more detail.”
This research is vital, he adds. “Wood vinegar definitely has potential for treating mould and bacterial films, but there’s a big issue around process and quality control. For example, if the pyrolysis temperatures are too high, the product can contain toxic aromatics, dioxins and chlorine-containing chemicals. If you’re applying the wood vinegar to crops, they’ll end up in the environment, which is something you certainly don’t want.”
Diverse feedstocks, multiple processes
This is just a flavour of the work that’s going on at EBRI, says Dr. Nowakowski. Other projects involve looking at other sorts of waste, including chicken manure, municipal solid waste, used cooking oil, spent barley grains from beer production, bicycle tyres, offcuts of aluminium-plastic “thermal covers” and cork as well as a scoping exercise for carbon sequestration using farmed seaweed.
And it’s not all about pyrolysis, either. When the feedstock contains a lot of water that would be too energy-intensive to remove – such as algae – they can use a process called hydrothermal liquefaction. This involves catalytic treatment of a liquid slurry, with the result being a “biocrude” similar to that obtained from pyrolysis of the solid material.
Biological processes such as anaerobic digestion and fermentation are also researched at EBRI, says Dr. Nowakowski. “When a feedstock has very low calorific value but contains some good sugars, then we can get microorganisms to convert it to methane or ethanol, which can then be used as a fuel. The advantage of this approach is that the end product is usually quite refined, making the analysis a lot simpler.”
In summary, it seems that EBRI has a solution for every challenge: “Whatever the feedstock type, we can select and tailor the process to extract the maximum value from it!” he says.
Expanding biowaste research – with support from Shimadzu
Through all of his work as a researcher and laboratory manager at EBRI, Shimadzu has been there for him, explains Dr. Nowakowski. “Right from 2013 when we were setting up the new laboratories for bioenergy research here at EBRI, I’ve been able to benefit from their expertise in analytical chemistry,” he states.
“They’ve always been ready to discuss our needs, and in many cases they’ve made a major contribution to the decision-making process. For example, in one project we needed to analyze permanent gases from our hydrothermal liquefaction unit, and they helped with setting up a GC-BID system – which significantly improved our research outputs compared to the GC-FID system we’d originally been planning.”
This collaboration has continued to the present day, he adds, with guidance on getting the most out of the equipment as well as routine maintenance and timely support. “With so many people booking our equipment, business continuity is very important for us – so it’s great that we always have a quick response from Shimadzu!” he says.
And it’s clear that there’s no let-up in the pace of work at EBRI. Dr. Nowakowski says that they’re still expanding their operations: “We’re increasingly focusing on applied research and novel processing methods, including biological processes for the production of value-added chemicals. We’re also becoming very strong in materials science, with emphasis on carbon materials derived from biochar. In addition, very recently EBRI started the development of an integrated laboratory-scale center to explore the production of low-carbon hydrogen from biomass.
There’s so much going on – and it’s good to know that Shimadzu will be there for us, ready to help with anything I need!” he concludes.
Researcher biography:
Dr. Daniel Nowakowski is a Lecturer in Chemical Engineering and Applied Chemistry at Aston University (Birmingham, UK), and Laboratory Manager of Aston’s Energy and Bioproducts Research Institute (EBRI). Following undergraduate studies in Chemical Technology in Gliwice (Poland), he completed his Ph.D. degree in Environmental Catalysis at the University of Leeds (UK) in 2007. The same year, he joined Aston University as a post-doctoral research assistant, and since 2012 he has held several senior fellowship posts. He has been an active researcher since 2007 and has been involved in a wide variety of research projects and collaborations relating to the processing, analysis and application of biomass and pyrolysis products.